Introduction
Corner separation is a three-dimensional separation occurring at the blade-endwall junction in aeronautical compressors. It is proven to originate from complex interactions of secondary flow structures (Horlock et al., 1966; Kang and Hirsch, 1991), and is one of the most limiting flow feature in modern aeronautical compressors in terms of efficiency and operability. More specifically, the azimuthal pressure gradient that exists between two consecutive blades causes the so–called passage flow in the near-endwall region. This flow drives low momentum fluid towards the suction side of one blade, which accumulates and leads to a high-loss region that can be prone to stall. This high-loss region can be characterised by the topology of the skin friction lines patterns (Délery, 2001). It is greatly influenced by the operating conditions, and notably by the inflow incidence (Taylor and Miller, 2017; Dawkins et al., 2021).
Corner separation is very sensitive to the channel geometry and can be influenced in different ways. The 3D stator design itself is of great importance (Harvey and Offord, 2008; Taylor and Miller, 2017) as well as the type of junctions with which it is embedded to the endwall. The presence and type of fillets and hub clearance can indeed significantly impact the corner separation (Goodhand and Miller, 2012; Sun et al., 2021). Non-axisymmetric endwall deformation can also be used to smoothly deflect the flow (Reutter et al., 2017) or act as an aerodynamic separator (Hergt et al., 2009). On top of these geometrical modifications, technological devices such as vortex generators or fences can be added (Hergt et al., 2011, 2013). This paper intends to provide a methodology that aims at studying a new type of control device, called “guide fin”, corresponding to one or several profiled fences of potentially non-conventional shape. The idea behind the guide fin is to provide a tuneable control device in between the vortex generator and the non-axisymmetric endwall, which can either lower the losses at near-design conditions or on a broad range of incidences.
In the present work, the guide fins are evaluated in a subsonic linear compressor cascade at the LMFA, Lyon. A key advantage of such a configuration is to allow detailed measurements that precisely characterise the corner separation (Ma et al., 2013; Zambonini et al., 2017; Dawkins et al., 2021). These works, as well as (Feng et al., 2015), showed that low fidelity computations such as RANS have difficulties in predicting the corner separation size. According to (Lei et al., 2008), RANS can predict two topologies of corner separations, referred to as closed and open. (Taylor and Miller, 2017) showed that at the critical incidence, a pair of saddle and focus critical points appears at the blade – endwall junction, and rapidly moves away from the blade suction side. As a consequence, the corner separation switches from the closed to the open topology, yielding a sudden increase in losses and blockage. However, (Dawkins et al., 2021) measured a smooth evolution of the experimental losses with the incidence, proving that the notion of critical incidence is purely numerical. Such a defect in RANS predictions can be explained by the anisotropy of the Reynolds stress tensor in the corner region (Gessner, 1973), not accounted for when using the Boussinesq hypothesis.
However, time-averaged friction lines from (Dawkins et al., 2021) show that this saddle/focus pair exists, but appears at an incidence between 0.8° and 2.3° in the baseline considered in this paper. Before the appearance of this pair, time-averaged friction lines are very similar to what RANS predicts, bringing confidence in RANS predictions at near-design incidences. Moreover, (Dawkins et al., 2021) showed that the flow anisotropy in the corner region increases with the incidence, together with total pressure losses. In this work, the studied control device aims at reducing the separation magnitude, which might help reducing the flow anisotropy. In other words, best guide fins in terms of loss reduction could be the best predicted ones. On the other hand, non-efficient guide fins could lead to similar loss over predictions than with the open topology, and would be discarded.
RANS could then be fitted to evaluate control devices that reduce the corner separation size. A RANS-based numerical methodology is thus proposed in this paper to explore the effect of numerous guide fins on a baseline configuration. It relies on an automated numerical chain in which parametrised guide fins are generated, included in a mesh of reference and evaluated using RANS computations. Two sub-domains of the design space are explored and several guide fins improving the flow at two incidences are found. Experimental measurements involving two of these guide fins are finally presented and validate the numerical methodology by showing a significant loss reduction.
Experimental set up
Baseline configuration
The experiments were performed in a subsonic cascade wind tunnel at the LMFA, Lyon, whose characteristics are precisely detailed by (Dawkins et al., 2021). This cascade is set in order to precisely control the inlet flow, which consists in the inlet endwall boundary layer, the inlet angle and the inlet turbulence. The cascade parameters are presented in Table 1. Bleeding channels are used to remove the boundary layer developing on the endwall 0.5 stator chord (c) upstream of the channels. For each flow condition, the bleeding flow is altered to retrieve the same pressure profile around the endwall leading edge. This set up ensures a thin and repeatable inlet boundary layer for all inflow conditions. This enables to observe a classical, repeatable corner separation behaviour downstream of the cascade. 25 pressure tapings are used to best fit the pressure distribution along the profile at midspan against a database of numerical flow predictions obtained at angle increments of 0.1. This enables to measure the inflow incidence with a precision of ± 0.05⁰ for the investigated blade. The inlet turbulence is generated by a grid 280 bar widths upstream of the cascade and measured 0.25c upstream of the leading edge of the blades.
Table 1.
Cascade Characteristics.
The performance of the cascade is measured with a five-hole probe
The integrated pressure losses
This baseline configuration is intended to be used as an open test case for corner separation studies, and was precisely designed and characterised by (Dawkins et al., 2021) for that purpose. The high aspect ratio of the blade is made on purpose to uncouple the midspan flow from the near-endwall flow and to isolate the corner separations occurring at the two roots of the blade. The midspan profile trailing edge separation starts at the incidence i = 5.5°, and develops further upstream as the incidence is increased. Moreover, endwall losses rapidly increase with the incidence, from approximately 0.9% at i = 0° to 4.3% at i = 5.4°, and are obtained with an experimental uncertainty of ±0.1%. This is shown later in the Results and Discussion section. As such, this precisely controlled cascade exhibits an important corner separation, and can therefore be used for evaluating a control device such as guide fins.
Guide fin manufacturing and insertion
An insertion system was designed to equip six neighbouring channels with guide fins, on both endwalls. It is made of a fixed part fitting the stator profile in which a removable part containing the guide fin can be slid in. Figure 2 illustrates this principle, and Figure 3 its implementation in the cascade. The system is 2 mm thick, yielding a section reduction of about 1.3%. Its upstream part starts at an axial position 0.29c upstream of the stator leading edge. It consists of a ramp that smoothly brings the flow up, from the endwall to the top of the platform, with an angle seen by the flow of 3.8°. This system, including the guide fin, is manufactured with a Fuse Deposition Modelling (FDM) method, using ABS plastic. A nozzle of 0.4 mm diameter is used, as well as a precision of 0.09 mm per layer. With this system, a complete set of 12 guide fins is manufactured in about 30 hours, which is much faster than with a conventional process. In order to limit extra losses and the inlet boundary layer thickening, the fixed part is sanded down to a rugosity of 0.5 µm. The same operating points are reached with and without the insertion system. Nonetheless, adding this system necessarily alter the reference flow. A flat platform was then slid in the insertion system to mimic the initial baseline configuration. This modified baseline is characterised experimentally by the authors, and is the one used in this paper. This way, the gain measured when replacing the flat platform by a platform with a guide fin is independent of the insertion system. Moreover, a variation of the endwall losses below the experimental uncertainty is found at several incidences when comparing the initial and modified baseline. This yields a negligible effect of the system.
Figure 2.
Illustration of the insertion system, with GF-4 and GF-16. U ∞ refers to the upstream velocity.
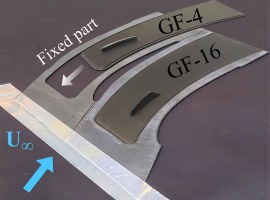
This experimental set up thus enables to assess the influence of a guide fin on endwall losses. Next section describes a RANS-based methodology implemented to find manufacturable guide fins that efficiently reduce the endwall losses.
Methodology for guide fin generation and evaluation
In order to evaluate numerically numerous guide fins of various shapes, an automated numerical chain is developed. It is composed of three main steps: guide fins parametrisation, mesh generation and CFD computation.
Guide fin parametrisation
In order to ensure an aerodynamic shape, the guide fin is built using several aerofoils stacked at different spanwise locations, from hub to tip. So as to reduce the total number of parameters, it is chosen to build only one parametrised aerofoil, whose parameters values are a function of its spanwise location. The evolution of each parameter is chosen to be linear, because it requires only two values and still allows the construction of complex geometries. Finally, two fillets can be added to round the junctions between the hub and the sides, and between the tip and the sides. Examples of guide fins generated with the following methodology are shown in Figure 4.
Aerofoil parametrisation
The parametrised aerofoil is built from a parametrised thickness law and a parametrised camber law. A thickness law of reference is built with the BEZIER-Parsec 3333 parametrisation described in (Salunke et al., 2014), in which geometrical parameters can be easily set and tuned. In order to stay close to the simplest thickness laws, no inflexion points are permitted. From then, the parametrised thickness law is obtained by tuning the maximum thickness value. A circular trailing edge (TE) is added so that the dimensioned aerofoil has a constant trailing edge thickness, fixed to the smallest manufacturable value shown in Table 2. Examples of thickness laws are shown in Figure 5. The camber law is obtained from a spline of order 2 constrained by three parameters: the position of the maximum of camber and the values of its tangents at the edges. Several examples are shown in Figure 6. Providing a chord value and a two-dimensional position is then sufficient to define an aerofoil with 7 parameters. Given a linear evolution, a hub aerofoil, a tip aerofoil and a height value define an entire guide fin with 15 parameters.
Fillets parametrisation
In the present work, fillets can have much larger radii than in conventional uses. Therefore, they can be used to either round the junctions or to deform the guide fin surface near them. The hub fillet is chosen to have a constant radius along the side surface and is therefore defined with one parameter. However, the radius of the tip fillet varies along the chord in order to avoid self-intersection. It varies from a fixed lowest value set by manufacturing constraints at the trailing edge up to a maximum value at the leading edge. A spline of order 3 is used to avoid curvature discontinuities at the LE. The maximum value is computed as the minimum radius of curvature of the tip aerofoil in its first 25% of chord. This criterion was found to correspond successfully to the largest fillet radius reachable before self-intersection in the leading edge region. The final geometry of the tip fillet can then be obtained with a single parameter, the percentage of the maximum fillet radius authorised at the tip leading edge.
Efficient design space exploration accounting for manufacturing constraints and design experience
The 17 degrees of freedom of the parametrised guide fins may lead to guide fins which are irrelevant in terms of aerodynamic expertise or do not respect manufacturing and positioning constraints (see Table 2). In order to reduce the design space to geometries of interest for the user, two new parametrisations are proposed with the following characteristics: (a) for all values of the new parameters, the associated value of the original 17 ones can be easily retrieved and (b) all geometries generated by the new parameters satisfy the manufacturing and positioning constraints. The first parametrisation involves only 4 new parameters presupposed to have a significant impact on the losses. This defines a relatively small subdomain easier to explore and mostly based on design experience. These 4 parameters correspond to the guide fin height, the inlet and outlet metal angles, and the curvilinear position on a midpitch line (see Figure 7) around a rather simple, two-dimensional aerofoil of reference. Their values is described in Table 3. The second parametrisation consists of 16 new parameters, allowing for more complex shapes. Guide fins can have very 3D geometries. Thin tip aerofoils and thin to thick hub aerofoils are considered. As tip fillet radii would be very small, no tip fillets are considered. Hub fillet radius varies between 0 and 75% of the guide fin height. Lean and sweep parameters varying between ±25° are introduced. The position of maximum camber varies in [30%
Table 3.
DOE-4 parameters range and value %c and % c G F refer to percentages of stator and guide fin chord.
Unfortunately, even these new parametrisations cannot guarantee that any geometry generated at random in these reduced design spaces will be associated with a RANS prediction. Indeed, the surface generation, the meshing process or the computation itself could fail in case of too complex geometries. In order to generate a design of experiments (DOE) which best explores the design space of admissible guide fins (i.e. with an available RANS result), an original and specific strategy for handling such computational failures is used. First, for each parametrisation, a large database of guide fins is generated using a Monte Carlo methodology and only the guide fins with viable CAD surfaces are kept. The main assumption in the algorithm used is that such large databases are representative of the set of all admissible geometries. The DOE is then built by picking a small subset which spans as best as possible the entire database. To achieve this, the “kernel herding” algorithm proposed by (Chen et al., 2010) is used. It consists in minimising the distance between the empirical distribution defined on the DOE and the one on the entire dataset. For the first parametrisation with 4 parameters, the corresponding DOE (DOE-4) with 40 geometries is shown in Figure 7. For the second parametrisation with 16 parameters, the corresponding DOE (DOE-16) contains 160 geometries. 5 of them are shown in Figure 8. Later in the paper, RANS results associated with each DOE are presented. Respectively 100% of the DOE-4 and 80% of the DOE-16 is successfully associated with a RANS result. These high viability rates ensure that both subdomains are indeed well explored.
Hybrid meshing strategy
In order to save computational time and to uncouple the spatial discretisation of the two geometries, the stator part is meshed separately from the guide fin part and is fixed. Attention is paid to generate these meshes consistently with one another. A structured O-4H mesh of a single channel of the baseline cascade is obtained using AutoGridV5 (Numeca). It contains approximately
CFD set up
RANS results are computed using the CFD solver elsA (ONERA). In order to validate the meshing methodology, results obtained on the fully structured mesh of reference and on the hybrid mesh without guide fin are compared in Figure 11, using the turbulence models of Spalart-Allmaras,
Results and discussion
Results of the design of experiments
Respectively 40 and 129 viable guide fins are selected for the DOE-4 and the DOE-16. The present work focuses on guide fins that act on a large range of incidences, while not deteriorating too much the losses at the design incidence. As guide fins are designed to act on the near-endwall losses, it is not relevant to evaluate them at incidences where separation at midspan occurs. As a consequence, endwall losses are monitored at an incidence near-design, i = 0.5°, and before the midspan separation, at i = 4.9°. Results are gathered in Figures 12 and 13, together with the RANS prediction of the baseline case for comparison purposes.
Results of DOE-4 show a widely spread cloud of points with guide fins that either deteriorate or improve the flow. No guide fin improves the flow on both objective functions compared to the baseline configuration, but several configurations dominate the others, in the Pareto sense. GF-4, in green, is particularly of interest as it significantly decreases the losses at high incidence without deteriorating too much the flow near design. Most of guide fins of the DOE-16 have a relatively low impact on the losses at near-design. This is consistent with its related design space, in which guide fins are forced to be relatively aligned with the local stator camber line. However, they are spread across a large range of losses at i = 4.9°. For the same reasons as GF-4, GF-16 appears to be particularly interesting.
In order to assess the ability of this RANS-based set up to find efficient guide fins with two different parametrisations, GF-4 and GF-16 are selected for experimental investigations.
Experimental validation
Table 4 gathers the experimental and RANS evaluations of GF-4 and GF-16. Experimental results confirm that both reduce or have a negligible effect on the endwall losses at 0.5°, and strongly reduce these losses at 4.9°. Notably, a maximum relative loss reduction of 36% is measured with GF-4. DOE-4 and DOE-16 thus enabled to find interesting guide fins that lower the losses. However, these guide fins appear less performant at 4.9° than expected.
Table 4.
Variation in endwall losses when adding GF-4 and GF-16. Predictions vs Experiments.
GF-16 is evaluated on more incidences for a more in-depth characterisation. Results are gathered in Figure 14. It appears that endwall losses are predicted to increase smoothly with the incidence. RANS predictions thus do not exhibit a critical incidence anymore, yielding an understandable over prediction of the gain in losses. Moreover, experimental endwall losses are decreased not only at 0.5° and 4.9°, but on a broad range of incidence from 0° to 5.9°. Notably, a net gain of 2.06%, corresponding to a relative gain of 47% is found experimentally at 5.4°, the last incidence before the midspan profile starts separating. GF-16 thus improves the robustness to stall while not degrading near-design losses.
Figure 15 compares the loss distributions predicted by RANS and measured downstream of the cascade, with and without guide fin at 0.5° and 4.9°. In the baseline case, RANS is found to under predict the corner separation at 0.5° and to over predict it at 4.9° with respect to experimental results. However, its spatial extension seems well captured. This is typical of a flow evolution before and after the critical incidence. On the other hand, predictions with GF-16 do not exhibit such an over prediction at 4.9°. This is consistent with the smooth evolution of the endwall losses and the absence of critical incidence in that case. Moreover, specific loss patterns are retrieved, such as the low loss region framed in black at 4.9° and the signature of the guide fin tip vortex pointed out by the black arrow at 0.5°. This confirms that the refinement levels in the experimental probe mesh and the numerical hybrid mesh are consistent with one another.
Figure 15.
Total pressure losses on the measurement plane 0.2c downstream of the cascade. Black rectangle: low loss region. Black arrow: signature of guide fin tip vortex. The investigated blade is on the left.

The implemented numerical methodology enabled to find interesting guide fins, using RANS predictions on two incidences. Adding a guide fin that reduces the losses is found to improve the prediction of the loss distribution downstream of the cascade. Therefore, the use of RANS is proven legitimate for finding efficient guide fins. Beyond the scope of this work, RANS seems promising for an optimisation process, in which the influence of more efficient guide fins could be better predicted.
Conclusions
In this paper, a numerical methodology based on RANS predictions of parametrised guide fins was presented. It was shown that this parametrisation could be efficiently tuned to restrain the explored design space according to the user experience. This could be done either by selecting several parameters pre-supposed to have a significant impact on the flow, or by constraining the aerodynamic characteristics of the explored guide fins. An automated hybrid meshing process enabled to mesh guide fins of various shapes consistently with a reference structured mesh obtained with AutoGridV5. This methodology was used together with dedicated algorithms to efficiently explore the design space. In total, 169 guide fins of various geometries were evaluated with RANS. The predictions of the two best guide fins are corroborated experimentally, both on endwall losses and loss distributions downstream of the cascade. Let us underline that DOE-4 was generated by varying four parameters pre-supposed to have a major impact on the endwall losses. As GF-4 enables to lower the losses, the height, the axial midpitch position and the inlet and outlet metal angles are likely to indeed play a major role in the corner separation control.
The well-known defect of RANS, yielding the notion of critical incidence was assessed on the baseline configuration. It appeared that this defect disappears for guide fins that efficiently improve the flow, thus justifying the use of RANS predictions to design such control devices. A nonphysical over prediction of the gain in losses at high incidence directly deriving from this defect was highlighted. However, important gains at high incidence were still found experimentally without degrading the losses near design. The operability of the stator is then successfully widened by these guide fins. Notably, a relative endwall loss reduction of 47% is measured at i = 5.4° with GF-16.
Perspective
Further investigations will be carried out in order to understand the effects of the guide fin shape on the flow. This could involve the coupling of this methodology with an optimisation process. If predictive enough, using metamodels could help ranking the influence of each shape parameter on the endwall losses.
Nomenclature
Axial coordinate
Pitch-wise coordinate
Spanwise coordinate
Re
Reynolds number, based on true chord
Upstream velocity
Boundary layer momentum thickness
Upstream total pressure
Upstream static pressure
Downstream total pressure
c
Stator chord
Guide fin chord
%c,
Percentage of stator or guide fin chord
Incidence
Critical incidence
Integrated total pressure losses
Profile total pressure losses
Endwall total pressure losses
Endwall losses variation with respect to the baseline case when adding GF-16
DOE
Design Of Experiments
RANS
Reynolds Averaged Navier Stokes
FDM
Fused Deposition Modelling
ABS
Acrylonitrile Butadiene Styrene
LE
Leading Edge
TE
Trailing Edge
LMFA
Laboratoire de Mécanique des Fluides et d’Acoustique
ONERA
Office National d’Etudes et Recherches Aérospatiales
elsA
ensemble logiciel de simulation en Aérodynamique