Introduction
Nowadays, gas turbine manufacturers have to meet ecological requirements, particularly reduction of NOX emissions. The most common way to meet these ecological requirements is to produce gas turbines that operate in the lean combustion regime. However, operation in the lean combustion regime makes the combustion system more prone to the occurrence of combustion instabilities 20, 10, 33, which may cause heavy damages. This requires prevention of combustion instabilities which, in turn, requires an understanding of the nature of their onset.
There are different methods and numerical tools for the prediction of combustion instabilities. The numerical tools used for thermoacoustic analysis could be divided into two large groups: frequency-domain analyses 21, 04 and time-domain simulations 23, 19. The first type of analysis is usually used in the linear analysis, i.e., to predict whether the setup is stable or not 04. It can also be used to predict the amplitude of unstable pressure fluctuations. To accomplish this task, 32 propose to perform simulations for each amplitude of acoustic oscillations that is characterised by its own FTF. The value of acoustic oscillation amplitude that corresponds to the zero growth rate is said to be the amplitude of saturated oscillations. The procedure requires performing a set of several simulations with different FTFs. On the contrary, using the time-domain analysis, both eventual unstable frequencies and their amplitudes are computed straightforwardly.
The straightforward way of the time-domain analysis of thermoacoustic instabilities would be performing unsteady CFD simulations of processes in gas turbine chambers with full complex geometries. Continuous improvement of computational capabilities of high-performance computing clusters makes this task possible 25, 35 but still computationally expensive. Thermoacoustic phenomena could be decoupled in processes of chemical reactions (combustion), turbulence and acoustics. Decoupling of turbulent combustion and acoustics is artificial, but it helps to simplify the analysis. Acoustic length and time scales are often considered to be much larger than chemical and turbulent scales. This makes possible to perform simulations of turbulent combustion and acoustics separately in two different tools.
First, we compute the response of the flame to low-amplitude acoustic excitations with the help of large eddy simulations (LES) using the thickened flame model of the AVBP code. As a result, the FTF 31, 16 of the setup is computed. Then, the obtained FTF is approximated with an analytical time-lag-distributed model.
Finally, we use a simplified wave-based approach implemented in Simulink to find the stability margins of parameters under which gas turbines could be operated without going into self-excited pressure oscillations. 19 have shown that thermoacoustic simulations in the time-domain using the wave-based approach with nonlinear flame model could predict different nonlinear behaviours of the system. The strong feature of the network model simulations in the time domain is that it is possible to predict the unstable frequencies of the system just knowing the FTF. And it is possible to predict the amplitude of these oscillations as soon as the flame describing function (FDF) — the response of the flame to velocity perturbations of various amplitudes 22 — is found.
In this study, we discuss an atmospheric single-burner test rig developed by Ansaldo Energia (AEN) and Centro Combustione Ambiente 26 equipped with one full-scale AEN gas turbine burner. Dependence of thermoacoustic stability of the setup on several parameters is discussed.
The article is structured as follows. First, the theoretical background of the three-step approach is explained. Second, the FTF calculated by LES is presented. Third, the calculated FTF is approximated by the time-lag-distributed model. Then, both linear and weakly nonlinear calculations are performed and the results are compared to the experimental ones. Finally, conclusions are given in the last section.
Background
Description of the large eddy simulations software for flame transfer function calculations
Recently, LES has been used to perform simulations of self-excited thermoacoustic instabilities 25, 35 and to perform forced simulations to determinate the FTF 25, 36. In this article, results of LES, particularly FTF, described by 26 are used. To improve reading of the article, the description of LES is provided. The reactive multi-species Navier-Stokes equations on unstructured grids are solved using a fully compressible explicit code AVBP 28. The viscous stress tensor, the heat diffusion vector and the species molecular transport use gradient approaches. The fluid viscosity follows the Sutherland law and the species diffusion coefficients are obtained using a constant specie Schmidt number and diffusion velocity corrections for mass conservation 09. A high-order finite element scheme is used for both time and space discretisation. The turbulent stress term is modelled by the classical Smagorinsky model 34. A chemical mechanism with six species (CH4, O2, CO2, CO, H2O and N2) and three reactions 27
is used to model methane/air combustion. The dynamic thickened flame model 05 is adopted to describe the iteration between turbulence and chemistry.
Usage of low-Mach number or “incompressible LES” 08 can give the advantage of shorter calculation times. Compressible LES are performed in this study, because in compressible LES, fewer approximations are made, thus they give more precise results.
Time-lag-distributed model for flame transfer function
In general, heat release rate Q oscillations of technically premixed swirl-stabilised flames depend on perturbations of velocity u and equivalence ratio φ 11
First, let us consider the response of the flame to upstream velocity perturbations. Once longitudinal acoustic wave reaches a burner swirler, it is divided into two components: oscillations of axial velocity and oscillations of tangential velocity. 17 have shown that the response of perfectly premixed swirl-stabilised flame to velocity fluctuations depends on both oscillations of two components of velocity — axial and tangential — and have proposed the time-lag-distributed model of the flame response to upstream velocity fluctuations.
where τi is the time delay of the corresponding mechanism, σi is the standard deviation of the corresponding time delay. The response of the flame to the axial perturbations of the velocity is modelled with the parameters τ1 and σ1. The parameters τ2, σ2, τ3 and σ3 model the response of the heat release to the tangential perturbations of the velocity produced by a swirler.
The physical meaning of the parameters τi and σi is understood if we switch from the frequency-domain representation of the FTF to its time-domain representation, i.e., to the unit impulse response (UIR). The UIR in this study is the response of the normalised heat release to the normalised velocity perturbation of unit amplitude. The analytical form of the UIR corresponding to the FTF of is
Thus, models the response of the heat release to acoustic oscillations with three Gaussians with mean values τi and standard deviations σi. The first Gaussian in described with pair of parameters τ1, σ1 models the time that fluid particles spend to travel from the zones where the flame is anchored to different points at the flame. Parameters τ2, σ2, τ3 and σ3 model the time that a fluid particle spends to travel from the swirler to the flame.
01 have shown that the equivalence ratio fluctuations influence the heat release through three mechanisms: change of the heat of reaction, change of the flame speed and change of the flame surface area. It can be seen from Figure 4 of 12 that the response of the turbulent flame to equivalence ratio fluctuations could be modelled similarly to and .
where parameters τ4, σ4, τ5 and σ5 together model the flame response to change of the heat of reaction and change of the flame speed, and parameters τ6 and σ6 model the flame response to area changes. Parameters τ4, σ4, τ5, σ5, τ6 and σ6 model the time that fluid particle spends to travel from the point of the fuel injection to different points at the flame.
Many gas turbines burners, including the burner under consideration, are designed in such way that the pressure drop of the gas through the burner is around one order of magnitude higher than the pressure drop of the air. In this case, the acoustic perturbations in the gas turbine combustion chamber excite oscillations of the air mass flow through the burner; meanwhile, the gas mass flow remains almost unperturbed. This allows to make an assumption that the equivalence ratio φ perturbations depend only on the air flow velocity u fluctuations in the burner 29
For such burners, it is possible to write a model for the total FTF.
where the fluctuations of the flame heat release rate Q′ depend only on the velocity fluctuations u′r at a reference position r upstream of the flame
At this point, the model for the FTF consists of 12 parameters and it could be cumbersome to determine all of them. However, for burners that have the fuel injection at the swirler blades, the values of the characteristic time delays modelled by parameters τ4 and τ6 are close to the values of the characteristic time delays modelled by parameters τ2 and τ3, respectively, and they cancel the resulting effect of each other. Thus, the model in can be further simplified using only four parameters 29, 06.
Two Gaussians described by and model in a simplified way the change of the heat release due to perturbations of the velocity themselves and due to perturbations of equivalence ratio, respectively. They have the same relative amplitudes because increasing the velocity of the flow by certain relative value or decreasing equivalence ratio by the same relative value would increase heat release by the same relative value.
Wave-based approach for thermoacoustic simulations
When the length of the setup under consideration is much larger than its dimensions in the other directions, it is possible to perform a one-dimensional low-order acoustic analysis 02, 30, 03, 15.
The test rig is considered as a set of sections with constant cross-sectional area. Pressure, velocity, temperature and density are decomposed into the sum of their mean component (denoted by ¯) and their fluctuating component (denoted by ′). Mean values of pressure, velocity, temperature, density and thermophysical properties are assumed to be constant along each section and are changing only from section to section.
Perturbations of pressure p, velocity u and density ρ in each section could be represented in terms of downstream and upstream propagating acoustic waves (characteristics) (see Figure 1):
where f and g are the downstream and upstream travelling components (Riemann invariants) of acoustic waves, respectively, and
In order to connect oscillating variables in different sections (see Figure 2), we need to know the jump conditions. To compute the jump conditions between sections separated by a compact acoustic element, such as sharp cross-sectional area change and a compact swirler, the system of linearised equations of conservation of mass and Bernoulli 07, 15 written in terms of f and g is solved.
where subscripts u and d denote the upstream and downstream sections, respectively. Matrices F and K take into account acoustic losses between sections; their coefficients can be found in .
To calculate the jump conditions at the flame, the system of linearised equations of conservation of momentum and energy (product of mass conservation equation and Bernoulli equation) written in terms of f and g is solved 07, 15.
where coefficients of matrices J and H can be found in . and are directly used in the network model time-domain simulations.
At the beginning of the first section and at the end of the last section, f and g waves are related by the reflection coefficients Rinlet and Routlet, respectively.
There are four main sources of acoustic losses: at cross-sectional area changes, at partially reflective boundaries, at acoustic boundary layers and due to viscose dissipation. In this study, only the first two mechanisms of acoustic losses are taken into account.
Since the network model is implemented in Simulink, it is possible to design and test both active and passive dampers of thermally driven acoustic oscillations in future work.
Step 1. Modelling the flame transfer function
Description of the experimental setup
The atmospheric test rig is characterised by two cylindrical volumes, the plenum and the combustion chamber, connected to each other by a full-scale industrial burner. A schematic view of the geometrical setup utilised for the thermoacoustic experimental campaign is shown in Figure 3.
A thick layer of refractory is interposed between the chamber walls and the external liner to make the test rig adiabatic. During the experimental session, it is possible to control air and fuel mass flow rate, as well as air temperature and the length of plenum and chamber. The length of the rig can be continuously varied in order to tune the frequency at which combustion instabilities occur. Further details about experimental setup can be found in the study by 26.
Description of the numerical setup
The LES computational domain is formed by a fully unstructured mesh of 11852789 tetrahedral elements. The mesh is refined in correspondence of the flame and mixing regions; the time step is 4×10−8 s, resulting in a Courant number equal to 0.7.
In order to reduce the computational costs and to be able to use a finer mesh in the flame region, the LES domain is shorter than the real combustion chamber (about one third of the real length). This assumption is considered acceptable since the recirculation zones are located well inside the LES domain; the flame is located in the first third of the LES domain; there is no diameter variation inside the test rig.
Inlet and outlet boundary conditions are imposed using the non-reflecting Navier-Stokes characteristic boundary condition formulation to control acoustic reflection 24. All the other walls are set as adiabatic and modelled using a logarithmic wall-law condition.
Flame transfer function numerical calculation
Once LES of the reactive process is statistically converged, a specific procedure to compute the FTF is performed. A multi-sinusoidal signal is imposed as velocity component normal to the burner inlet 26. This signal is applied both at the diagonal and at the axial inlet to excite heat release oscillations. Velocity excitations normalised by the respective mean velocities are identical in the both diagonal and axial channels of the burner. When velocity perturbations pass through the blades of diagonal and axial swirlers, tangential perturbations of velocity are produced. The frequencies imposed in the multi-sinusoidal signal are chosen in a wide range of frequencies that permit to determine the shape of the FTF with reasonable accuracy and focused on the frequencies of interest of the industrial burner.
The velocity fluctuations are recorded by numerical probes. These probes are located both in the axial and in the diagonal passages, as shown in Figure 4. Specifically, the velocity fluctuations recorded by these probes have been normalised against their own average values. The heat release fluctuations are computed as a global value of whole combustion chamber. The simulation is run for a time to guarantee at least six periods of oscillations at the lowest frequency of excitation. Frequencies are reported in terms of Strouhal number, which is calculated taking the inner diameter of the combustion chamber and the average velocity at the exit of the burner as the reference length and velocity, respectively. The FTF is calculated for each frequency imposed in the multi-sinusoidal signal and is shown in Figure 5.
Step 2. Analytical model for the flame transfer function
Optimum values of parameters τi and σi of the FTF modelled with are computed approximating the FTF calculated with LES using the method of least squares. Values of τi and σi normalised with respect to mean flow velocity at the burner exit and the diameter of the combustion chamber are presented in Table 1 and the corresponding model of the FTF is shown in Figure 5.
Step 3. Stability analysis using wave-based approach
Low-order network model setup
The numerical setup has been divided into six regions with three jump conditions with pressure losses, one jump condition at the flame and two boundary conditions as shown in Figure 6. The values of the cross-sectional area normalised against the cross-sectional area of the combustion chamber, the lengths of the sections normalised by the reference length and the temperature normalised by the temperature of the air at the inlet for each section are listed in Table 2. The jump matrices to connect acoustic waves between sections are calculated using and . The reflection coefficient of the inlet is taken Rinlet. The outlet reflection coefficient Rout,1 is measured experimentally using multi-microphone technique. Several values of the outlet reflection coefficient around the measured one are tested in this study because of some uncertainties in this value, particularly caused by microphones cooling. The normalised total length of the combustor (sum of the lengths of Sections 5 and 6) is varied in the range Lc.c.=0.741÷1.593 with the step of ΔLc.c.=0.037. Acoustic losses at area changes between plenum and burner and between burner and combustor are taken into account by pressure loss coefficients ζdecr=0.442 and ζdecr=0.718, respectively, calculated by the formulae proposed by 13. Acoustic losses at the swirler are obtained from the measurements. The active flame, i.e., the unsteady heat release, in the low-order network model is positioned at xfl=0.1. This value corresponds to the maximum of the heat release in the longitudinal direction in LES. Mean temperature is uniform in the first five sections. The temperature gradient coincides with the position of the active flame and is situated between Sections 5 and 6.
Results of linear network model simulations
For each set of parameters, the simulation is run for 0.3 s that is enough to observe whether the pressure oscillations grow or decay in time. The setup is excited at the inlet for first texc=0.1 s by the broadband excitation in the range of Strouhal number 0÷7.53 with the maximum amplitude of the signal 5 Pa. After 0.1 s till 0.3 s, the system is left to evolve by itself without external excitations. We make use of a parameter called cycle increment that gives information about the thermoacoustic stability of the system. It is possible to calculate the cycle increment from the time-domain simulations assuming the following law for the pressure perturbations:
where fi is one of the frequencies of pressure oscillations after texc, n is the number of the frequencies of pressure oscillations after texc, Pi is the amplitude of pressure oscillations at fi at the time texc, θi is the phase of the pressure oscillations at fi and αi is the cycle increment of the mode fi. Positive values of the cycle increment parameter αi indicate that the system is unstable, and the negative values of αi mean that the system is stable.
The frequencies of oscillations and their cycle increments are computed by approximating the time history of the pressure oscillations by using the least-squares method. In the simulations presented in this study, either one or none unstable frequency per run is detected, thus n=1 for all simulations in the network model.
Dominant frequencies of pressure oscillations and their cycle increments for various lengths of the combustion chamber are shown in Figure 7. Frequencies are normalised with respect to the mean flow velocity at the burner exit and the diameter of the combustion chamber. The dominant frequency of oscillations decreases while increasing the length of the combustion chamber. This indicates the acoustic nature of the modes computed in this study. The calculated frequencies agree well with the experimentally observed frequencies.
Figure 7.
Dominant frequencies of the pressure oscillations and their cycle increments for various lengths of the combustion chamber.
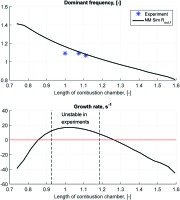
Thermoacoustic instabilities were observed in experiments in the range of combustion chamber length Lc.c.=0.93÷1.19. Simulations in the network model capture the unstable behaviour of the system qualitatively and predict the setup to be unstable for the slightly wider range of the values of the normalised combustion chamber length in Lc.c.=0.85÷1.30 (see Figure 7).
Results of weakly nonlinear network model simulations
It is possible to perform a weakly nonlinear analysis using the network model and the nonlinear heat release model. To do so, it is necessary to know the FDF — the response of the heat release to acoustic perturbations of different frequencies and different amplitudes. Since there is no available computed FDF of the setup, it is possible to mimic the nonlinear flame dynamics assuming the dependence of the parameters τi and σi on the normalised amplitude of velocity perturbations A upstream the flame. It was observed in a laboratory setup 14 that while increasing the amplitude of velocity excitation, the peak of the heat release distribution along the longitudinal axis was shifted towards the burner and the heat release distribution along the longitudinal axis became wider, i.e., the flame length was augmented. This means that when the amplitude of velocity perturbations upstream the flame is increasing, parameters τi are decreasing and parameters σi are increasing:
Square decay of τi parameters and linear increase of σi parameters gave smaller norms of residuals in 14 and are used in this study as well. Ratios of the second terms to the first terms of Equations (19a) and (20a) are taken the same as in 14. Absolute values of the second terms in Equations (19b) and (20b) are the same as in Equations (19a) and (20a), respectively.
When the amplitude of velocity perturbations approaches 0, values of τi and σi modelled by and approach values in Table 1, i.e., the FDF becomes the FTF computed by LES.
The network model setup is excited at the inlet by the same signal as in the linear analysis for first texc=0.1 s. After 0.1 s till 1.0 s, the system is left to evolve by itself without external excitations that is enough to reach either saturation to limit cycle pressure oscillations or infinitesimal pressure fluctuations. The maximum amplitudes of the pressure oscillations measured in the last 100 ms of simulations are plotted in Figure 8. Simulations are performed for the range of the combustion chamber length that are predicted to be unstable by the linear analysis and for three values of the outlet reflection coefficient Rout,1, 0.97Rout,1, and 0.94Rout,1.
Unstable frequencies of the pressure oscillations in the weakly nonlinear analysis are the same as in the linear analysis shown in Figure 7. Nonlinear simulations capture well the trend of experimental dependence of the pressure oscillations amplitude on the length of the combustion chamber (see Figure 8) with the assumed nonlinear model of the FDF. Simulations employing the outlet reflection coefficient reduced by 6% with respect to the measured value give a good match with experimental data.
Conclusions and current work
In this study, a three-step analysis of combustion instabilities in the time domain has been applied to an industrial atmospheric test rig. The first step consists in obtaining the FTF of the system by means of LES. The second step is to approximate the FTF obtained in the first step with the time-lag-distributed model for the technically premixed swirl-stabilised flames. The third step is to perform time-domain simulations using wave-based approach implemented in Simulink with the FTF from the second step.
The results of simulations using the three-step method show that it can be used successfully for the stability analysis. Simulations are run in the same range of the combustion chamber length as in the experiments. The unstable frequencies computed in the simulations match the unstable frequencies observed in the experiments. Simulations predict setup to be unstable in a slightly wider range of combustion chamber length than in the experiments, probably because of uncertainties in the outlet reflection coefficient measurements.
The amplitudes of pressure oscillations computed with the nonlinear analysis for different values of combustion chamber length capture the behaviour observed in experiments.
Currently, less costly Unsteady Reynolds-Averaged Navier-Stokes (URANS) simulations are being performed to compute the FTF for larger number of frequencies and to calculate the FDF of the setup. A future development of this study is to take into consideration of entropy waves propagation.
Appendices
Appendix A.
Appendix A. Matrices for jump conditions between network model sections
Matrices for jump conditions between sections for the case of area decrease are
where S is the cross-sectional area, M is the mean Mach number and ζ is the pressure loss coefficient.
Matrices for jump conditions between sections for the case of area increase are
Matrices for jump conditions between sections for the case of temperature jump with active flame and constant cross-sectional area are
where γ is the heat capacity ratio.