Introduction
One of the major optimization goals for the turbofan (TF) is the specific fuel consumption (SFC). In the last decades the SFC of the specific engine decreased based on the progression of single components. The benefits of the lower SFC on pollutant emissions was also a goal but not the main focus. During the last years the focal point changed. Furthermore, the regulations are limiting the future impact of aero engines on climate change. Based on the TF, MTU Aero Engines AG is developing the new Water-Enhanced Turbofan (WET) concept described by Schmitz et al. (2020). With the injection of high steam loads in the combustor, the enthalpy is increased and the peak temperature is decreased. The exhaust is cooled with a steam generator and the steam is liquefied through a condenser. The liquid water is separated, pressurized and passed through the steam generator and steam turbine before it is injected into the combustion chamber. Compared to a state-of-the-art aero engine, this concept potentially decreases NOx emissions by 90% and contrails by
Numerical simulations are a cost-effective method for predicting combustion processes. This requires both a chemical mechanism and a combustion model. Chemical mechanisms of kerosene have been intensively researched over a wide range of operating conditions (Ranzi et al., 2005). The POLIMI mechanism for kerosene is provided by the CRECK modeling group of the Politecnico di Milano (POLIMI), which is considered detailed due to the number of species and reaction equations involved. Ranzi et al. (1995, 2005) have shown a wide range of inlet temperatures, pressures and equivalence ratios and compared it to different experimental sources. The laminar flame speed, ignition times and species production were investigated and the mechanism demonstrated a global agreement. The mechanism is valid for a large temperature range and well represents the formation of nitrogen oxides. The POLIMI can therefore be considered as a reference. Dagaut (2002) provided another detailed mechanism for heavy hydrocarbon fuels based on experimental data of a jet-stirred reactor (JSR). In a subsequent study, the mechanism was reduced and optimized for high pressure conditions using additional available experiments (Dagaut and Cathonnet, 2006). Due to the application for aero engine conditions with high pressures both mechanisms are included in this study. However, in many cases such a large number of species and reactions is not necessary or affordable for the considered application. For this reason, reduced mechanisms are established. Luche (2003) reduced the Dagaut mechanism (Dagaut, 2002) to a skeletal mechanism. This limits the applicability of the mechanism, but significantly reduces the computational cost. None of the available chemical mechanisms for kerosene combustion are particularly validated for ultra WET conditions. The high steam contents, however, have a significant influence on the chemistry as shown by previous researches Schimek et al. (2013), Göke (2012) and Hiestermann et al. (2022). Thus, based on the detailed POLIMI mechanism, the performance of the other mechanisms mentioned for the considered ultra WET condition is evaluated within this study.
The investigation of skeletal up to detailed mechanism necessitates the use of a combustion model that achieves tolerable computing times in industrial applications. Tabulated chemistry such as the flamelet-generated manifold (FGM) combustion model allows the use of complex chemical mechanisms at moderate computational cost, especially when compared with finite-rate chemistry (FRC) as shown by Yang et al. (2017) and Panchal et al. (2019). In contrast, FRC transports the species involved in the chemical mechanism and solves them directly in the simulation. This results in high accuracy at high computational cost, depending on the mechanism. However, this time advantage refers to only one of the three sub-aspects that are necessary for a numerical solution: Pre-processing, processing and post-processing. The pre-processing step of the FGM approach can be time intensive due to required tabulation of the chemistry. The thermo-chemical state is tabulated over the full range of independent variables by solving one-dimensional flames. The flamelets resulting from the one-dimensional flame describe the source term of the combustion and are therefore essential. Various configurations are conceivable: For premixed combustion, it is straightforward to use freely propagating or counterflow premixed flames. In aero engine applications, however, various technically premixed to swirl-stabilized diffusion flames are frequently used (Hassa, 2013). The present study addresses the question if it is beneficial to employ the significantly more challenging counterflow diffusion flame model for the tabulation (Ramaekers et al., 2005), especially for ultra WET conditions. Hansinger et al. (2017) compared freely propagating premixed and counterflow diffusion flamelets for a non-premixed application under atmospheric conditions with natural gas. Surprisingly, the results obtained with premixed flamelets were superior when compared to the experimental measurements. However, a comparison between premixed and non-premixed flamelets for aero engine and ultra WET conditions is not found in the literature. Moreover, separate investigations of both are rarely seen in detail. Furthermore, the general influence of steam on flamelets has not been investigated yet. The present study follows a approach similar to Hansinger et al. (2017), but for the entire range of dry to ultra WET aero engine conditions.
Regardless of the employed flame model, the generated manifolds depend on the progress variable and mixture fraction, which are both independent look-up variables. Ihme et al. (2012) summarized several definitions of the variable from different authors. Ma (2016), Ihme and Pitsch (2008) and Pitsch and Ihme (2005) carried out a parameter study for different progress variable definitions for natural gas at atmospheric conditions based on H2O, CO, H2 and CO2. Fiorina et al. (2003, 2005a,b) proposed a general definition of the progress variable for dry combustion based on CO and CO2. In the present study new definitions of progress variables, which are adapted to the considered ultra WET conditions, are compared to established definitions.
In order to verify the observations and results obtained previously, a CFD-FGM analysis is carried out. For this purpose, the Sandia Flame D is used with the original settings to validate the implemented combustion model and manifold approaches. The Sandia Flame D burner is a widely used experimental facility for validating numerical combustion models (Barlow and Frank, 1998; Schneider et al., 2003; Barlow et al., 2005). The experimental facility is designed to study turbulent combustion and jet flame break-up in a controlled laboratory environment and the effects of various factors such as turbulence intensity, equivalence ratio distribution, and chemical mechanisms on the combustion process. The main focus in this work is the analysis of ultra WET conditions. However, experimental results for ultra WET combustion with kerosene are not available in the literature, therefore the Sandia Flame D is adapted to the new operating conditions. The characteristic of the original Sandia Flame D and the dry aero engine simulation are compared. With the verification of the setup, influences such as jet break-up, axial velocity and temperature distribution are analyzed under dry and ultra WET conditions in FGM large eddy simulations (LES) with premixed and non-premixed look-up tables.
Chemical mechanism
A variety of chemical mechanisms for kerosene have been studied and validated. Especially in the last decades, the available experimental database has grown significantly (Dagaut and Cathonnet, 2006). Therefore, mechanisms have been optimized for various equivalence ratios, inlet temperatures and pressures. One of the most detailed mechanism is the POLIMI by the CRECK modeling group Ranzi et al. (2012, 2014, 2015) and Bagheri et al. (2020). Generated by the lumping procedures their mechanism includes specifications from low (LT) and high temperature (HT) oxidation, as well as the inclusion of NOx and soot. The mechanism used here combines the variants except for the soot formation shown in Table 1. With
Table 1.
Chemical mechanisms for long-chain hydrocarbon fuel.
[i] aLuche (2003).
[ii] bDagaut and Cathonnet (2006).
[iii] cDagaut (2002).
[iv] dRanzi et al. (2012, 2014, 2015).
One of the mechanisms being studied for influence under ultra high steam is established by Dagaut (2002). The original low pressure Dagaut mechanism (DagLP) has been validated for a equivalence ratio
As the next gradation of chemical mechanisms the Luche (2003) is added to the study. As a skeletal mechanism the Luche includes fewer reaction equations and species shown in Table 1. At all there are three different version of the Luche mechanism available that only differ from the threshold on the flux of N species (Cerfacs, 2023). Independently of this, the three mechanism are valid for a equivalence ratio from
The analysis is divided into two sub-aspects i.e., the laminar flame speed and the mole fraction at constant adiabatic flame temperature for dry and wet conditions. Both are influenced by the reaction kinetics for each chemical mechanism. For an application in a real gas turbine, especially the laminar flame speed is essential. The laminar flame speed affects flame shape and is important for predicting flame stability. Therefore, the influence of steam depending on the mechanism is investigated. Another value in assessing the mechanism is the formation of intermediate and product species. The major species CO and CO2 are therefore analyzed under ultra WET conditions.
Operating points
The challenging operating conditions in an aero engine combustion chamber have an influence on the analysis requirements. Both the long-chain hydrocarbon fuel kerosene and the high pressure are influencing factors. In addition, the inlet temperature is high, which increases the thermal loads in the combustion chamber. The WET concept addresses these issues by counteracting the thermal loads with the injection of significant amounts of steam. The considered operating points for dry to ultra WET conditions are defined in Table 2.
They are representative for an aero engine according to the WET concept. The ultra WET combustion operating conditions are described using the water-gas ratio (WGR) in Equation (1), which defines the relationship between water and the sum of water and air. It is used here primarily to define the steam content at the inlet.
Laminar flame speed
The laminar flame speed in Figure 1 is computed by solving a freely propagating one-dimensional premixed flame at a fixed adiabatic flame temperature of
Figure 1.
Laminar flame speed vs. equivalence ratio WGR symbols: (+ WGR = 0.00), (
WGR = 0.10), (
WGR = 0.20), (
WGR = 0.30), chemical mechanism colors: (
Luche), (
DagHP), (
DagLP), (
POLIMI), Tad = 1,800 K, Tin = 600 K, p = 20 bar.
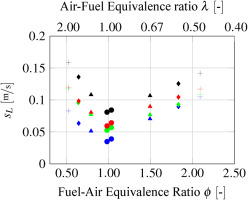
Figure 2.
Adiabatic flame temperature vs. equivalence ratio for (One-Step
), (Luche, DagLP and DagHP
) and (Polimi +) with WGR 0.0, 0.1, 0.2, 0.3 Tin = 600 K, p = 20 bar.
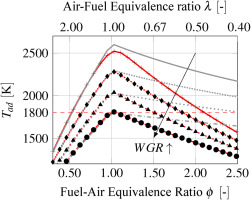
In the lean range, the relative discrepancy for the skeletal and detailed mechanisms related to the POLIMI is constant. Another observation is that the laminar flame speeds computed with the Luche mechanism are closer to the DagHP at high equivalence ratios. It is therefore understood that at a constant flame temperature, the laminar speed decreases in the lean region and increases in the rich region. Thus, the steam changes the local conditions of the flame. Especially if the results are compared with dry conditions (Wu et al., 2018). A direct comparison of the DagLP with the DagHP provides a result that was not to be expected. In terms of laminar flame speed, the optimized DagHP for high pressure applications exhibits greater discrepancies with the POLIMI than the DagLP.
Concentration of carbon monoxide and dioxide
Figure 3 shows the mole fraction of the dissociation of CO and CO2 across the flame front. Generally speaking, the temperature reduction caused by steam addition promotes the exothermic CO2 production. To eliminate this dominant effect, the molar fractions are analyzed at constant adiabatic temperature for the dry and ultra wet conditions in the rich region.
Figure 3.
Mole fraction vs. normalized length of CO (
) and CO2 (
), chemical mechanism colors: (
Luche), (
DagHP), (
DagLP), (
POLIMI), Tad = 1,800 K, Tin = 600 K, p = 20 bar. (a) Dry combustion WGR = 0.00 at ϕ = 2.09. (b) Ultra WET combustion WGR = 0.30 at ϕ = 1.03.
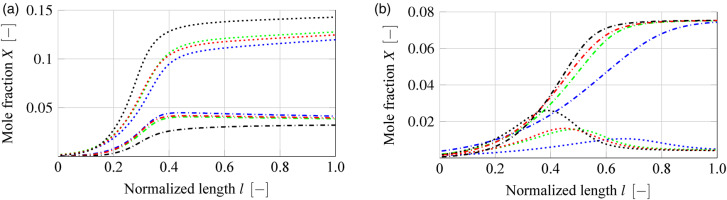
In Figure 3(a) the profile of CO2 from POLIMI differs and is lower compared to the others. With less complexity in the mechanism, the local CO2 production of the other mechanisms is overestimated. The opposite is shown for CO. The DagHP shows a slightly better agreement for both mole fractions. Differences in the distribution exist especially for CO under ultra WET conditions, see Figure 3(b). This behavior is based on the steam injection and the almost stoichiometric equivalence ratio. With a lower ratio of O2 to C the production of carbon monoxides and dioxides is less independent of the mechanism. However, under dry conditions, CO production should dominate over CO2 even with the same equivalence ratios. Therefore, the shift in the order of production rates is due to the effect of H2O on the reaction kinetics. The wet conditions additionally lead to a change in the preferred mechanism to DagLP. The Luche mechanism shows significantly greater deviation in WET combustion.
In conclusion, for the present operating points, the DagLP best matches the laminar flame speeds and mole fraction profiles at ultra WET aero engine conditions obtained with the POLIMI. As the latter is considered to be too time-consuming in the pre-processing step for industrial applications, the DagLP is used in the following. The other mechanisms are not explored further in the present investigation. The reason for this is that since the chemistry is based on table generation of the flamelets, it can be assumed that similar behavior is expected in the three-dimensional simulation.
Flame configuration
The flamelet assumption describes a turbulent flame as an agglomeration of thin, locally one dimensional, laminar flame elements (Peters, 1984, 1988; Peters and Kee, 1987). This assumption is the basis for a variety of flame models. A comparison between the non-premixed and premixed flames is made using two types of model flames, see Figure 4. The freely propagating flame is a simplified approach to generate the flamelet database. In contrast, the non-premixed counterflow diffusion flame is significantly more complex and time-consuming in the pre-processing step. The one-dimensional premixed flame is simulated with a freely propagating flame, where a perfect mixture of oxidizer, fuel and additional steam is provided at the inlet on the left side in Figure 4(a). The velocity at the inlet is equal to the laminar flame speed in order that the flame front position remains fixed.
The inlets of the counterflow diffusion flame are divided into fuel and oxidizer with additional steam, as shown in Figure 4(a). The steam is added to the oxidizer stream only. The two separate streams form a stagnation plane. The flame stabilizes between the stagnation point and the oxidizer inlet based on the inlet fluxes. Contrary to the premixed configuration, the entire range of possible mixture fractions is found within the domain.
In order to solve the equations for both flames a combination of Cantera (Goodwin et al., 2022) and the open source code Ember (Speth, 2022) is implemented in the pre-processing program with custom modifications. Therefore, a switch between a steady-state Cantera and unsteady simulation Ember can be automatically conducted with user defined functions.
Flamelet table variables
The mixture fraction and the normalized progress variable are the two independent variables that describe the flamelets. The mixture fraction is formulated according to Bilger (1980a,b, 1989). The Bilger coefficient
The value
where
The second independent variable is called normalized progress variable. For this purpose, the progress variable is introduced first. In order that the progress of the combustion can be defined, the progress variable
The progress variable is based on the definition of Ma (2016) with weighting factors w and the mass fractions Y of water, carbon dioxide, hydrogen and carbon monoxide defined in Equation (5).
A direct comparison and a simple application in the numerical solver is facilitated by normalizing the progress variable C. Above all, the direct comparison of different variables is possible. The manilds are used as evaluation criterion with C.
The determination of the weighting factors w and the species considered depends mainly on the fuel and the operating conditions. It is necessary to verify which definition describes the manifolds in an optimal manner.
Premixed: freely propagating flame
If the premixed flames are compared with the non-premixed flames, the difference becomes apparent as soon as the flamelets are created. One-dimensional premixed flames describe the changes of the thermo-chemical state of a perfectly premixed gas depending on the axial position x until complete combustion of the mixture. For each freely propagating flame in Figure 4(a), the mixture fraction at the inlet is fixed. Thus the entire
Figure 5.
Temperature vs. mixture fraction of premixed freely propagating flame and counterflow diffusion flame with normalized progress variable isolines. (a) Freely propagating flames. (b) Counterflow diffusion flames for steady and unsteady branches.
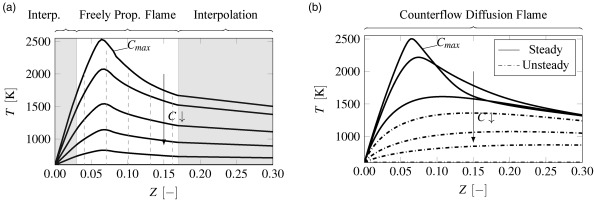
The lean and rich flammability limits of a premixed flame limit the available Z range. In the present study mixture fractions in the range
Non-premixed: counterflow diffusion flame
A one-dimensional counterflow diffusion flame describes a single non-premixed flamelet at a specific strain rate. In contrast to the premixed flame, a single flame covers the entire mixture fraction range. However, for the description of the whole C–Z space a single flamelet is not sufficient. To simulate further flamelets, the method of strain rate increase is applied. The flame is quenched at the higher strain rate until the flame is extinguished due to the high velocities. This is illustrated by various normalized progress variable isolines in Figure 5(b).
The simulation of the whole C–Z space is separated in two parts. In the steady state approach the flamelets are calculated beginning from a strain rate
Progress variable study
Progress variable requirements
The definition of the progress variable is not unique but the choice is based on some principles proposed by Ihme et al. (2012). The definition of C should result in a reasonable transport equation. This transport equation is used in the numerical simulation with the FGM model to solve the combustion. The included reactive species should represent the combustion process in comparable time scales. Moreover, the description of C and Z represents the thermodynamic and chemical space. Therefore, the involved parameters should represent the entire framework. Also is it necessary that the parameters are independent for the definition of the manifolds. More details are shown in the publication of Ihme et al. (2012). Another criterion is the characteristic of the slope of the progress variable. Due to the representation of the combustion process it is desirable that C has a moderate continuous slope. This guarantees that the entire combustion process is represented without large discretization uncertainties.
Progress variable definition
As mentioned earlier, the definition of the progress variable is fundamental for the description of the manifold and the chemical source term. Following to Ma (2016) and Pitsch and Ihme (2005) in Equation (4), different weighting coefficients are assigned. A total of 5 sets of coefficients are examined to weight the respective mass fraction listed in Table 3. The definition by Ma (2016) weight the water content by a factor of
Table 3.
Progress variable definition.
Case Name | ||||
---|---|---|---|---|
MaCa | 4.00 | 2.00 | 0.50 | 1.00 |
DryNGCb | 0.00 | 1.00 | 0.00 | 1.00 |
WETC1 | 0.00 | 1.00 | 0.50 | 1.00 |
WETC2 | 0.00 | 1.00 | 0.75 | 1.00 |
WETC3 | 0.00 | 2.00 | 0.50 | 1.00 |
[i] aMa (2016).
[ii] bFiorina et al. (2003, 2005a,b).
Figure 6.
Molar fraction vs. equivalence ratio for (H2O
), (H2
), (CO
) and (CO2
) at Dry WGR 0.0 and ultra WET conditions 0.3 Tin = 600 K, p = 20 bar. (a) Dry combustion WGR = 0.00. (b) Ultra WET combustion WGR = 0.30.
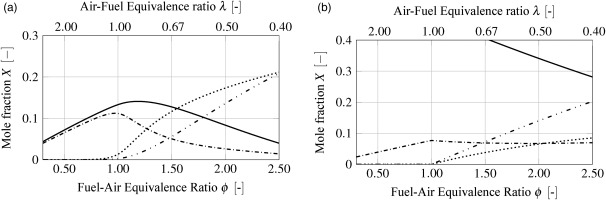
The results differ with the injection of steam. The decrease in temperature influences both exo- and endothermic reactions. After the stoichiometric point CO2 remains constant while CO is still increasing as shown in Figure 6(b). Moreover, CO2 and CO no longer balance each other. To address this effect at high WGR, H2 is added in the progress variable definitions WETC1 and WETC2. WETC1 and WETC2 differ only in the weighting factor of hydrogen. The progress variable definition WETC3 allows a proper comparison to the description of Ma (2016), as it only differs in the weighting factor for H2O.
The source term of the progress variable is illustrated by color in the
Figure 7.
Parameter study: Normalized progress variable source term of premixed flamelets Tin = 600 K, p = 20 bar and WGR = 0.3. (a) MaC (Ma, 2016). (b) DryNGC (Fiorina et al., 2003, 2005a,b). (c) WETC1. (d) WETC2. (e) WETC3.

In contrast to the qualitative consideration in Figure 7 the second derivative of
Progress variable source term distribution
Dry combustion
The normalized source term of the progress variable is illustrated in Figure 9 with a threshold to show only the area of interest. Under dry conditions differences are seen especially in the mixture fraction. Due to diffusion and the mixing between the oxidizer and fuel the non-premixed flamelets extend to higher Z values. Nerveless, the reaction area is smaller compared to the premixed. The deviation shown has no influence on the stoichiometric point. As a result, the position of the maximum value of the source term is identical for dry non-premixed and premixed flamelets.
Figure 9.
Normalized progress variable source term of premixed and non-premixed flamelets WETC2 at dry combustion condition Tin = 600 K, p = 20 bar and WGR = 0.0. (a) Premixed. (b) Non-Premixed.
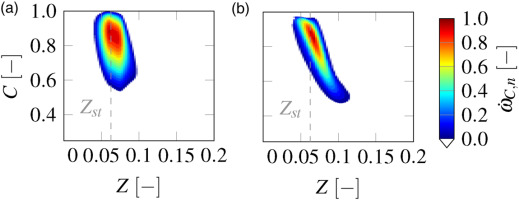
If the results shown in Figures 9(a) and 9(b) are compared with Hansinger et al. (2017) the differences are significant. The discrepancy may result from two aspects i.e., the higher pressure and inlet temperature at aero engine conditions in the present study. Qiao et al. (2021) have shown for a different fuel that increasing the pressure and temperature results in a further expansion of the maximum temperature depending on the strain rate. For high pressures, the maximum temperature is increasing while the strain rate is increasing. Therefore, the pressure increase has an effect mainly on the counterflow diffusion flame used in the non-premixed case. The increase in temperatures results in a constant maximum temperature at higher strain rates. It is assumed that this effect also occurs with the fuel kerosene. As a result the quenching strain rate increases with higher pressures and inlet temperatures. Thus, the formation of the flamelets in the non-premixed case is more influenced compared to the premixed case. The impact is seen in an expansion of the source term of the non-premixed flamelets to lower progress variable values in Figure 9(b). In addition, the applied fuel is different which has also an influence on different characteristics of the flamelets.
WET combustion
Under WET conditions, the generation of non-premixed flamelets in particular involves a certain amount of user effort compared to premixed flamelets. The Steam injection reduces the steady branch of the non-premixed flamelets, where the unsteady branch has a higher impact. Figure 10 shows the influence of steam injection with a WGR of
Figure 10.
Normalized progress variable source term of premixed and non-premixed flamelets WETC2 at WET combustion condition Tin = 600 K, p = 20 bar and WGR = 0.1. (a) Premixed. (b) Non-Premixed.

Figures 11(a) and 11(b) illustrate the representation of the different manifolds at a WGR of
Figure 11.
Normalized progress variable source term of premixed and non-premixed flamelets WETC2 at WET combustion condition Tin = 600 K, p = 20 bar and WGR = 0.2. (a) Premixed. (b) Non-Premixed.
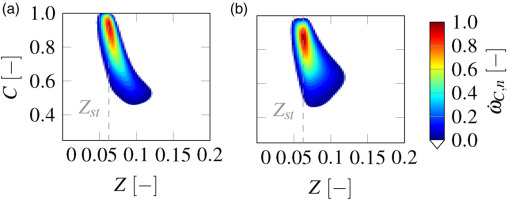
The source terms for ultra WET conditions at
Numerical verification case
Sandia flame D
In order to verify the progress variable approach and illustrate the three-dimensional effects of the premixed and non-premixed flamelets an academic jet flame “Sandia Flame” by Barlow and Frank (1998), Barlow et al. (2005) and Schneider et al. (2003) is used. They experimentally investigated the flame on various operating points and provided the data in the International Workshop on Measurement and Computation of Turbulent Flames (TNF) (TNF, 2023). In this work the configuration Sandia Flame D, a methane-air flame, is used for the validation of the numerical modelling. In addition, the verification process is carried out in three stages. First, the numerical model is validated using the original Sandia Flame D configuration. This is done by comparing the numerical results of the premixed and non-premixed flames with the experimental results. Subsequently, the aero engine relevant dry operating conditions are set. To characterize the behavior of the premixed and non-premixed flamelets, the results from the dry case are compared with the original Sandia Flame D case. Finally, steam is injected and the effect on the premixed and non-premixed manifolds is analyzed. This procedure ensures that a first statement about the behavior of premixed and non-premixed flamelets in aero engine applications with high steam is possible without an additional experiment.
Validation case and numerical setup
The Sandia Flame D is a piloted coaxial turbulent methane-air diffusion flame with three inlet streams. The main jet is characterized by a equivalence ratio of
Table 4.
Simulation cases.
To simulate the reacting flow, the FGM combustion model mentioned above is implemented in OpenFOAM. The two independent variables
Results
Methane-air sandia flame D
With respect to the flame structure, the instantaneous distribution of velocity and temperature, as well as the corresponding mean values, are considered quantitatively. Similar structures can be seen in the velocity distributions of the premixed and non-premixed results in Figures 13(a) and 13(b). The instantaneous snapshot shows the vorticities of the jet. In the mean field it is evident that the break-up widens the jet and increases the temperature and velocity fluctuations. This behavior can be seen in both cases. Nerveless, the penetration depth is lower with premixed flamelets. It follows that the break-up of the jet is evident at low axial positions and the kinetic energy of the vortices dissipates earlier.
Figure 13.
Instantaneous (left) and mean (right) axial velocity and temperature distribution of Sandia Flame D. (a) Premixed axial velocity distribution. (b) Non-premixed axial velocity distribution. (c) Premixed temperature distribution. (d) Non-premixed temperature distribution.
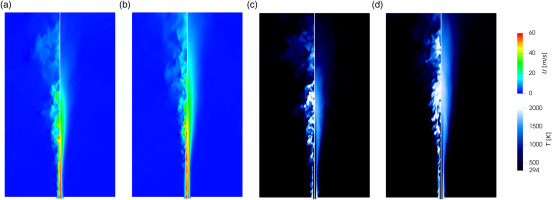
For the validation of the numerical model, certain axial positions along the main flow direction are used. In order to consider the full range, the radial temperature and axial velocity distributions are shown over the axial positions x/D = 3, 7.5, 15 and 30. Figure 14 shows a good agreement between the non-premixed and the experimental results with an error of less than
Kerosene-air sandia flame
The focus in this paper is on the application of premixed and non-premixed flamelets in aero engine conditions, especially with high steam content. For this purpose, the generated flamelets are first examined under dry conditions. Three things in particular are discussed here: The influence of the high temperature, the high pressure and the characteristics of kerosene.
The DryAEC conditions in Figure 16 show a wider radial velocity and temperature expansion and therefore, a break-up of the main jet at a lower axial position. The process of the jet break-up is influenced by various factors, including the fuel and oxidizer properties, turbulence intensity and chemistry. Close to the nozzle of the burner, Kelvin-Helmholtz instabilities occur between the co-flow and pilot stream in both simulations. Due to the higher ratio of the pilot and co-flow temperature the intensity of this phenomenon is greater than in the methane case discussed above. Apart from that, the axial expansion of the temperature is lower, which indicates the influence of high pressure, fuel characteristics and inlet temperature.
Figure 16.
Instantaneous (left) and mean (right) axial velocity and temperature distribution of DryAEC Sandia Flame. (a) Premixed axial velocity distribution. (b) Non-premixed axial velocity distribution. (c) Premixed temperature distribution. (d) Non-premixed temperature distribution.
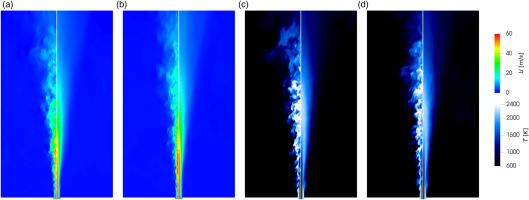
With the exception of x/D = 3, there are no major differences in the trend of the velocity profiles shown in Figure 17. This can be explained by the fact that the inlet velocities are the same as those of the Sandia Flame D. At
Kerosene-air-steam sandia flame
The additional steam significantly decreases the flame length. When steam is injected, the equivalence ratio at the main inlet is kept constant and the mass of the fuel-air mixture is reduced by the amount of steam. This consideration inevitably results in a reduction of the thermal power. As a result, the impulse in the domain is reduced. The opposite approach, where the thermal power is independent of the amount of steam, is explored by Hiestermann et al. (2022).
For the WET conditions the flame had to be stabilized by a higher equivalence ratio at the pilot inlet. The reason for that is the strong reduction of the adiabatic flame temperature due to the high amount of steam on the oxidizer side. This is shown in Figure 2. Compared to the previous simulation, it is noticeable that the premixed and non-premixed results are significantly closer to each other in Figure 19. The addition of steam has the effect that the thermal diffusivity is increased by a higher specific heat capacity of the mixture. The difference in the assumption of a freely propagating flame and a counter flow diffusion flame is thus reduced. This is supported by the similar penetration depth of the jet into the domain as well as the absolute axial length of the temperature distribution. Likewise of the counterplots are the radial velocity profilesin Figure 20. As in the previous observation, the trend is similar to that of the Sandia Flame D. However, it should be noted that the peak of the velocity at x/D = 30 is lower compared to the dry case. This occurs even though the inlet velocities are identical. The temperature profiles show a slight offset between the two flamelet variants illustrated in Figure 21.
Conclusion
This study focuses on the influence of the selected one-dimensional model flame setup for flamelet-generated manifold (FGM) combustion large eddy simulations (LES) at ultra WET aero engine conditions. Various mechanisms for kerosene combustion investigated at aero engine conditions represent the influence of steam injection on the reaction kinetics with different degrees of accuracy. Even for detailed mechanisms, like Dagaut (Dagaut, 2002; Dagaut and Cathonnet, 2006) and POLIMI (Ranzi et al., 1995, 2005), the predicted laminar flame speeds and particularly the obtained inner flame structures differ considerably. Hence, special attention must be paid to the selection of a reaction mechanism for ultra WET aero engine conditions.
The choice of the progress variable definition, especially the adjustment of the weighting coefficients for the species mass fractions, is crucial for a good representation of the manifolds. This study reveals that a single set of weighting factors is not sufficient for all considered dry to ultra WET aero engine operating conditions. We showed that particularly for ultra WET conditions a specific combination of H2, CO and CO2 results in a well-defined progress variable.
The comparison of the premixed freely propagating flame and the non-premixed counter flow diffusion flame shows a effect of the flamelet models. One of the essential conclusion is that steam is affecting the distribution and magnitude of the source term. As the amount of steam increases, the difference between premixed and non-premixed flamelets decreases.
Based on FGM-LES of a customized Sandia Flame D setup we demonstrate, that the influence of the choice of one-dimensional model flame on the CFD results varies, depending on the fuel and operating conditions. Using non-premixed flamelets is superior for the original Sandia Flame D case with methane. For an adapted kerosene Sandia Flame at aero engine conditions, however, both flamelet models yield almost identical result, especially at ultra WET conditions. The non-premixed flamelet approach is thus more reliable, but at the price of higher numerical and user effort compared to the premixed flamelet approach. While our results suggest, that at certain operating conditions premixed flamelets provide comparably good accuracy, the generalizability of this observation is still open to further research.
As a further study, the effect of steam on the strain rate sensitivity of premixed one-dimensional flames should be investigated. For this purpose, the model of the premixed counterflow flame can be applied to analyze strain rate. For the general application of premixed flamelets for dry and ultra WET aero engine condition, more configuration and operating points should be investigated. Furthermore, experiments should be carried out to validate the numerical model approaches for wet combustion.
Nomenclature
Roman letters
Speed of sound (m s1)
Progress variable weighting factor (−)
Specific heat capacity (m s−2)
Scaled progress variable (−)
Diffusion coefficient (m2 s−1)
Diffusion mass fluxes (kmol m−2 s−1)
Number of atoms (−)
Pressure (bar)
Coordinate r axes (m)
Time (s)
Temperature (K)
Adiabatic flame temperature (K)
Molar enthalpy (J mol−1)
Velocity component x (m s1)
Axial velocity component (m s1)
Velocity component y (m s1)
Progress variable weighting factor (−)
Atomic mass (kg kmol−1)
Coordinate x axes (m)
Molar fraction (−)
Coordinate y axes (m)
Mass fraction (−)
Progress variable (kmol kg−1)
Coordinate z axes (m)
Mixture fraction (−)
Greek letters
Mass density (kg m−3)
Cylindrical/Cartesian factor (−)
Bilger coefficient (−)
Non-dimensional strain rate (−)
Thermal conductivity (W m−1 K−1)
Air-Fuel equivalence ratio (−)
Dynamic viscosity (kg m s−1)
Kinematic viscosity (m2 s−1)
Unsteady factor (−)
Molar production rate of species k (kg m−3 s−1))
Progress variable source term (kg m−3 s−1)
Fuel-Air equivalence ratio or equivalence ratio (−)
Appendix A. Governing Equations for Flamelets
The flamelets equations are based on the three-dimensional governing equations. With the assumption of axisymmetric stagnation flow the formulation can be reduced to one-dimensional equations, which describes the flamelets (Kee et al., 2017). In general the flamelet structures are a function of time represented by the value
The energy Equation (10) and species Equation (9) includes the diffusive fluxes. In Equation (11) the species diffusive mass fluxes