Introduction
In recent years, with the development of aviation power systems, electric-driven distributed propulsion systems have become a research hotspot and have been applied to small and medium-sized aircraft (Yang et al., 2021). Compared to the traditional propulsion engine using fossil fuel, the all-electrical energy propulsion system has a great advantage in energy-using efficiency, operational cost, the environmental influence. In the thin-haul aviation operation, Dramatic reductions in energy costs are anticipated by Distributed Electric Propulsion (DEP) aircraft instead of aircraft with the conventional propulsion system by almost 84%. Moreover, the energy cost has cut operating costs by nearly 31% (Kim et al., 2018). Moreover, it also significantly increases the nose plane taking off and landing and the emissions of incomplete combustion products like CO2, SO2, NO2, and so on. A ducted fan driven by electricity is an important equipment for the electric propulsion system. Comparing standard rotors and propellers, ducted fans of the same size not only can produce stronger power and less noise (Wick et al., 2015), and its flow in the edge of blades is easier controlled (Perry et al., 2018), but also make an aerodynamic structure more compact, improve the safety performance and lower noisy sound due to the ring effect of the duct (Li and Gao, 2005). It dramatically benefits the aircraft whole efficiency, capability, and flight stability.
The optimization of aerodynamic design of fan blades has been a topic of interest for several decades. In 1926, Mark et al. introduced a novel turbomachinery design system, T-AXI, which incorporated a duct fan blade geometry generator that allowed for the visualization and calculation of the aerodynamic characteristics of various blade components (Turner et al., 2010). Recently, Nsukka et al. proposed a simplified method for designing fan blade bases using conformal transformations based on the Zhukovsky transformation. Additionally, in 2019, Denton introduced the open-source turbomachinery aerodynamic design platform (Multall), which includes a meanline design module, blade geometry generator, and a 3D flow solver (Denton, 2017). To assess the fidelity of the Multall solver in simulating internal flow in low-speed turbomachinery, Piero et al. utilized the Multall 18.3 software to predict the steady-state flow field in the annular sector of a 315 mm tubular axial fan (Danieli et al., 2021). The results indicated that the predicted pressure curve and the aerothermal efficiency tendency were in good agreement with experimental data, as well as with results from the state-of-the-art commercial software. Various optimization methods have been employed in the design of fan blades, leading to improved efficiency and performance. For instance, Cho used the gradient optimization method to design a ducted fan blade with the same efficiency but a 30% larger tip clearance (Cho et al., 2009). In general, most optimization methods rely on gradient or fuzzy positive correlation in search of an optimal design, and the curse of dimensionality remains a key problem. For turbomachines with tens of design parameters per blade row, numerous trials are required to search for an optimal design. Thus, adopting high-fidelity simulations in the optimization process for even a medium number of design parameters can be computationally expensive and time-consuming.
One emerging approach is the so-called “active subspace optimization method,” which identifies the primary direction in a design space, and quite promising progress was achieved in several gas-turbine-related applications. For instance, Ashley et al. established a subspace to design temperature probes with the goal to minimize hysteresis pressure loss and the ratio variation with Mach number. They obtained a relatively excellent temperature probe design (Scillitoe et al., 2020) by weighing the impact of design parameters on the design goal using linear combination weights. Additionally, Pranay used the active subspace method to reduce the dimensionality of a 25-dimensional fan blade design space to a 2-dimensional active subspace (Seshadri et al., 2018). They then created 2D contour maps to visualize the relationship between four target variables: cruise efficiency, cruise pressure ratio, maximum climb flow capacity, and sensitivity to fan manufacturing errors. Based on these maps, they recommended optimizing the blade design by exploring the high-dimensional design space. More recently, Wang et al. and Wei et al. applied the active subspace method to the uncertainty quantification (Wang et al., 2020, 2021) and design optimization (Wei et al., 2023) in turbulent combustion. The scope of the paper is to take a further step and develop a toolkit for rapid optimization of turbomachinery blade using the active subspace method and Multall turbomachinery design platform. Four main steps of the methodology involve the following:
Results and discussion
A previously designed ducted fan for general aviation was selected to demonstrate the effectiveness of the proposed method. This section is oriented as follows: The first subsection describes the development of a Python-based numerical framework. This software platform allows one to model the performance of the ducted fan using numerical methods. Using Python, one can automate many of the calculations and explore the design space quickly. The second subsection defines the target design space. It involves specifying the range of values for each design parameter, such as reaction, flow coefficient, workload, fan diameter, etc., sampling over the design space of interest, and generating a set of candidate designs. The third subsection analyses sensitivity, including analysing how does the sample size affect active subspace dimensions or eigenvalues. The fourth subsection focuses on constructing and solving the optimization equation. It involves using mathematical techniques to construct an equation that relates the active subspace variables to the adiabatic efficiency of the ducted fan. One can then solve this equation to find the optimal values of the design variables that maximize adiabatic efficiency. The last subsection documents the results of the optimal aerodynamic design.
Numerical framework
All the CFD results reported in this paper were obtained using the Multall turbomachinery design system in-house flow solver. The system comprises of three related programs developed using FORTRAN77: MEAGEN, STAGEN, and a 3D solver. MEAGEN performs a 1D calculation to obtain velocity triangles, set annulus boundaries, generate initial blade shapes, and twist them for a free/forced vortex design. The output file from MEAGEN serves as an input file for STAGEN, which defines the blade shapes. The 3D blade is generated by stacking and combining 2D blade shapes into stages. Finally, the Multall system reads the input file written by STAGEN and performs a 3D multistage calculation to predict the detailed flow pattern and overall performance. The roadmap of the design system is shown in Figure 1.
To automate the process, it would be beneficial to integrate the Multall turbomachinery design system within a Python-based blade optimization framework. One way to achieve this is by using function libraries, which are simple and cost-effective. Using a dynamic link library (DLL) instead of a static link library allows for repeated calls without wasting resources and can be changed without recompiling. Given the system’s structure, it is necessary to convert the three linked programs into DLLs, each corresponding to a specific aspect of the system. The main program can then call these DLLs in sequence, as shown in Figure 2. This approach enables more seamless integration of the Multall design suite with the Python-based optimization framework, making it easier for users to design and optimize turbomachinery blades.
Target design space and sampling strategy
This section describes the exercise conducted on a single-stage ducted fan. It focuses on generating multiple blade-shape design samples using Gaussian random sampling. First, a design space of 16 parameters is established, listed in Table 1. The blade-shape design parameters serve as input parameters, while the three aero-thermal performance metrics are objectives to train the active subspace. This approach helps identify the most critical input parameters that impact the performance metrics most, allowing for more efficient optimization of blade designs.
Table 1.
List of design parameters and sampling space.
The design parameters are defined around normal values and sampled using Gaussian random sampling with N = 344. The range of each parameter is listed in Table 1. Each sample set
As to the sample size requirement, the size of samples must be larger or equal to
Active subspace identificaiton
This study carried out active subspaces for three critical aero-thermal parameters of the ducted fan. The first objective is to optimize the adiabatic efficiency of the single-stage fan, which is the primary focus of the study. The second objective is the flow capacity of the fan, which is restricted in this study. The third objective is to ensure that the pressure ratio of the fan is equal to the pressure ratio of the baseline design.
In term of adiabatic efficiency
An active subspace for adiabatic efficiency is sought to capture its variation in 16-dimensional space with fewer dimensions. The goal is to construct an active subspace that reduces the dimensionality to the expected dimension, which is determined by evaluating the gap in the eigenvalues (Constantine, 2015).
The first step is to calculate the subspace eigenvalues of each dimension using gradient decomposition. If gradients are not available, finite difference approximations can be used to obtain approximate values of the gradient. In this study, the small design space makes it feasible to use finite difference approximations. eigenvalues
The main idea behind subspace dimensionality reduction is to use matrix multiplication between the input parameter vector and a tall transformed matrix, reducing the high dimensionality of m to a lower dimensional s. The transform
(5)
Furthermore, Figure 4 shows the relationship between the forward map
In term of mass flow rate
Following the same procedure, the active subspace for mass flow is identified. Same as the adiabatic efficiency, the largest gap between adjacent eigenvalues in the scenario of mass flow also lies between the 1st and 2nd index, shown in Figure 5(a). Additionally, a single dimension also yields the smallest error, shown in Figure 5(b). Lastly, the transform matrix,
In term of pressure ratio
Lastly, the active subspace for the total-to-total pressure ratio is identified. Similarly, the largest gap between adjacent eigenvalues in the scenario of total-to-total pressure ratio also lies between the 1st and 2nd index, shown in Figure 6(a), and a single dimension yields the smallest error, shown in Figure 6(b). Lastly, a linear connection between the subspace
Figure 6.
The eigenvalues (a), subspce errors (b) and scatters of pressure ratio (c) in pressure ratio active subspace.

(7)
To summarize, this section discusses the use of active subspaces to identify dominant directions in a high-dimensional design space. By using this technique, the authors were able to reduce the dimensionality of the design space and identify the most significant design parameters affecting the performance of a ducted fan. Results show that active subspace exists for fan adiabatic efficiency, mass flow rate, and total-to-total pressure, and the most suitable dimension for all three parameters is one. For adiabatic efficiency, a manifold relationship between the subspace and adiabatic efficiency is observed, where the adiabatic efficiency varies as a quadratic function curve along a single vector in the 16-dimensional design space. A fairly linear connection between the subspace and the parameter is concluded for mass flow and total-to-total pressure ratio.
Fidelity analysis
Despite the promising result presented in the above section, questions remain such as independence of the active subspaces, sensitivity of parameters, and accuracy of manifold modelling. This section investigates the fidelity of the active subspace approach. First, to verify the independence of the previously identified active subspaces, additional data samples can be generated randomly in the design space and used to compute the subspaces again. If the resulting subspaces are similar to those computed earlier using the limited number of samples, it can be concluded that the subspaces are independent of the specific data samples used and represent the dominant direction of the objective in the whole design space. To investigate the sensitivity of various design parameters, the gradient of the objective function for each design parameter can be calculated using the active subspace. This will provide insight into which design parameters impact the objective most and can be used to guide the optimization process. Lastly, a manifold model can be fitted to the data in the active subspace, which can be done using linear regression for a linear model or polynomial regression for a quadratic model. The accuracy and fitness of the model can be evaluated using statistical metrics such as the R-squared value and mean squared error.
Independence of active subspace
Two questions need to be addressed to verify the independence of the active subspaces from the data samples. The first question is whether the active subspaces would differ with different sample contents for the same sample size, and the second question is whether the sample size can affect the result of the active subspaces. This section uses a series of samples of different sample counts to investigate the effect of the sample size on the active subspaces. The recommended sample size
Figure 7.
The independence verification for adiabatic efficiency subspace: eigenvalues (a), subspace errors (b) and eigenvector components (c).
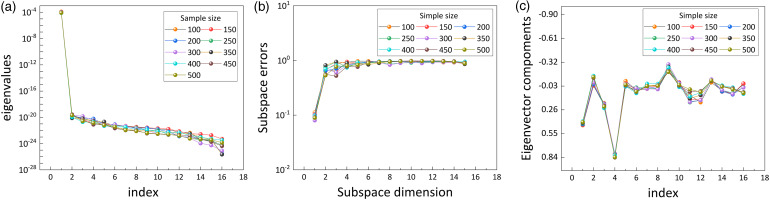
Additionally, the independence of the mass flow rate subspace is also shown in Figure 8. Figures 8(a) and 8(b) demonstrate no significant difference in the existing eigenvalues and subspace errors for each dimension among different sample sizes. The subspace components also fluctuate only slightly within a very small range. Lastly, Figure 9 shows that the pressure ratio subspace is almost unaffected by the training samples, as the curve remains the same as the sample size increases. These results demonstrate that the active subspaces discussed in Section 2.3 are independent of the data samples used in the calculation process.
Sensitivity analysis in terms of parameters
In Section 2.4.1, it is demonstrated that the elements of transformed matrices
Fitting curve of active subspace
This section uses polynomial fitting to build fitting curves in the active subspaces. Polynomial fitting aims to establish a functional relationship between the map
where n can be any positive integer.
The scatter plots in Figures 4(a), 5(c), and 6(c) show the distribution of design samples in each active subspace. Based on these scatter plots, linear or quadratic responses may fit the trend of the scatter distribution very well. Therefore, using first-order polynomial and secondary-order polynomial to fit the objectives
To compute the coefficients associated with the models, Equations (9) and (10) are built using samples. To choose the best function curve fitting the plots, the correlation coefficients of the two functions in all active subspaces must be compared. Figure 11(a) compares the correlation coefficients of the first-order and second-order polynomials with different sample sizes in the efficiency subspace. The graph shows that the line of the second-order polynomial fitting is above that of the first-order polynomial from beginning to end, indicating that the quadratic curve has a stronger correction of sample scatters in the efficiency subspace. Furthermore, the quadratic curve tends to be stable, and the coefficients in the line still drop as the sample size increases. Thus, the second-order polynomial fitting is chosen, and the related coefficients are computed using Equation (11).
Figure 11.
Correlation coefficients of two fitting curves in different sample size: adiabatic efficiency (a), mass flow (b) and pressure ratio (c).
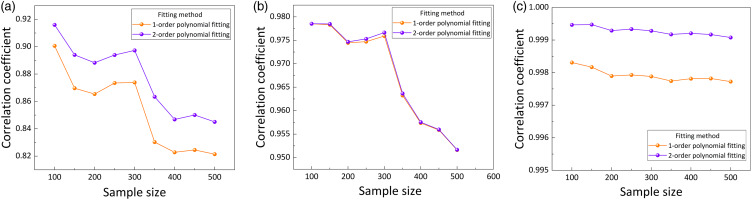
where
where
Optimization of a single-stage fan blade
This section focuses on optimizing a single-stage fan blade with specific parameters shown in Table 1. Using the Multall solver, the adiabatic efficiency, mass flow, and pressure ratio of the fan are computed as 93.401%, 92.022 kg/s, and 1.202, respectively. The main objective of the optimization is to maximize the adiabatic efficiency while keeping the mass flow and pressure ratio constant. An equation group that includes constraint equations from the mass flow and pressure ratio active spaces and an objective equation from the efficiency space is constructed to achieve this objective. The equation assembly is presented in Equation (14).
Prio to solving the above equation assembly, it is important to analyze the monotonicity of the objective function with respect to the constraints. By examining the plot of the quadratic function, it is evident that the objective function first increases and then decreases at the axis of symmetry
This optimization problem is solved using the simplex algorithm, and the resulting design vector
Furthermore, Equation (14) can be transformed as a group of indefinite equations, shown in Equation (17).
Since three equations can only solve for three unknowns, the three most sensitive parameters – radius, first-row deviation angle, and loading coefficient – are selected as unknowns in Equation (17). The other parameters are considered as known values obtained by average random sampling in the design space. However, it was found that Equation (17) was difficult to solve by directly sampling the entire design space. Only a small region in the design space could be mapped to 1.20471 or greater in the efficiency active subspace. Therefore, an effective method was to limit the sample space to the vicinity of
Lastly, a total of thirty sets of unknowns were sampled using average random sampling, and by solving Equation (17), 30 optimized fan designs were produced. The aero-thermal performances of these designs were then calculated using the Multall solver, and the results are shown in Figure 13. Figure 13(a) shows that the adiabatic efficiency of the optimized fans was, on average, higher than that of the baseline design, but it did not reach the highest theoretical efficiency. Some issues with the fitting curves may need to be addressed to improve efficiency further. Figure 13(b) indicates that the mass flow of the optimized fans was slightly different from the base mass flow, but it centered around 90.656. Based on this result, the authors proposed changing the aimed mass flow from 92.022 to 93.388, as mass flow has a strong linear changing tendency. On the other hand, the pressure ratios of the optimized fans remained largely unchanged compared to those of the base fan, as shown in Figure 13(c). To correct the target value of the indefinite equation, the authors first noticed that the scatter distribution on the horizontal axis in Figure 11(a) was limited below 0.8, which made the fitting curve heavily dependent on the data below 0.8 and imprecise at the largest value point. To address this issue, the authors set groups of random aimed values above 0.8 of
Figure 13.
Aero-thermal proformance of 20 optimized fans: adiabatic efficiency (a), mass flow (b) and pressure ratio (c).
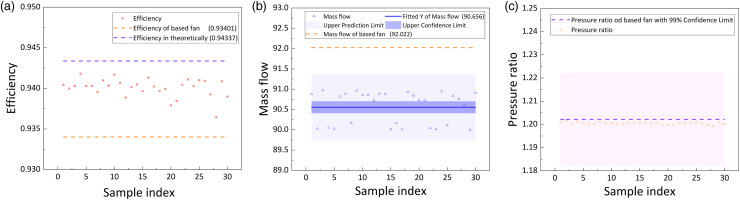
After implementing the corrections discussed above, Figure 14(a) plots the fitting curve of the efficiency, which was generated using 200 new special samples, and an excellent result was obtained, as seen in Figure 14(b), where the mass flow was around the base value of 92.022 with a 95% confidence limit zone. The fitting function is described in Equation (18).
The best value point of this function was found to be 0.82, which corresponded to the highest efficiency of 94.21%. As a result, the value of 0.82 was set as the final aimed value of
Table 2.
Aero-thermal performance of the optimized fan designs.
Finally, the blade design with the highest efficiency was chosen as the optimal design, with an adiabatic efficiency of 0.944, mass flow of 92.164, and pressure ratio of 1.203. The primary parameters of the optimized fan are presented in Table 3. Additionally, the blade shape parameters obtained from the optimization process are used to generate a profile file by recalling a customized Multall solver, which includes the 3D coordinates of the stator and rotor. Matlab codes are then used to convert the profile file into a format that can be used in Solidworks software. The resulting 3D model of the optimized ducted fan is presented in Figure 15.
Table 3.
Design choices for the optimized fan blade.
Conclusions
The preliminary design of turbomachinery aerodynamics traditionally relies heavily on the engineer’s experience, which can be a time-consuming and inaccurate process. To address this challenge, this paper proposes a novel optimization strategy for turbomachinery aerodynamic preliminary design using active subspace. The method utilizes active subspace techniques to reduce the dimensionality of the design space, making efficient and accurate exploration of the space possible. The proposed method was applied to a single-stage fan, where the goal was to optimize the adiabatic efficiency while keeping the mass flow and pressure ratio constant. The following key findings were highlighted:
The active subspace optimization method is robust and efficient, requiring minimal trial cost to quickly optimize the aerodynamic design of the single-stage fan blade.
The active subspace can be calculated independently of the training sample calculation process.
The active subspace represents the primary direction in which the objective changes the most, while the orthogonal direction remains steady, allowing for efficient optimization in a low-dimensional space.
Nomenclature
the vector of blade parameters for the jth training sample
the vector of the lower boundary for design space
the vector of the upper boundary for design space
the vector of standard deviation in Gaussian random sampling
the vector of average in Gaussian random sampling
the vector of normalized
the forward map of