Introduction
A common approach to improve the thermal efficiency is by further increasing the turbine entry temperature. Engine components such as turbine blades are directly affected by higher thermal stresses and need to be cooled internally with bleed air. This has led to sophisticated multi-pass cooling designs in which a balance between the reduction of coolant consumption and sufficient cooling to prevent a decrease in lifespan is pursued. A thorough understanding of the underlying heat transfer processes under engine-similar conditions will unlock the potential for optimised designs with lower fuel consumption and will result in more efficient and thus sustainable aero engines. As regards to turbine blades, rotation leads to Coriolis and centrifugal buoyancy forces which alter the secondary flow field within the cooling channel (Han, 2013). This results in a different heat transfer pattern for the pressure and suction sides of the channel compared with the non-rotating frame, consequently overcooling one channel side and overheating the opposite side, depending on the radial outflow or inflow of the passage.
The recent review by Ekkad and Singh (2021a) identified the knowledge gap left by the classical temperature measurement approach based on heated copper segments, which can only provide area-averaged data. Meanwhile, more advanced thermal diagnostic techniques, such as transient liquid crystal thermography, can address this limitation and have been validated against steady-state methods (Lorenzon and Casarsa, 2020), confirming its reliability as it gains popularity within the gas turbine cooling community (see Ekkad and Singh (2021b)). In this context, Waidmann et al. (2016) presented a novel rotating rig facility (RotRig) to investigate convectively cooled turbine blades through the application of thermochromic liquid crystals (TLC). In Waidmann et al. (2018) two-dimensional heat transfer results under rotating conditions were introduced for the first time. Building upon the aforementioned work, new data reduction methods consisting of line-averaging and region-based heat transfer histograms were presented by Waidmann et al. (2022) and applied in Gutiérrez de Arcos et al. (2022) in a case study under different channel orientations and rotation numbers. The later studies were expanded in Gutiérrez de Arcos et al. (2024) with enhanced data representation methods and an experimental uncertainty estimation. Considering purely numerical investigations on internal cooling channels under rotation, Göhring et al. (2016) obtained accurate heat transfer predictions using RANS with the shear stress transport (SST) turbulence model in combination with the curvature correction and reattachment modification options available in ANSYS CFX for a benchmark case from literature (Wagner et al., 1991). Later, they expanded their investigation by assessing the time-changing buoyancy effects from the experiment and their impact on heat transfer with an URANS approach (Göhring et al., 2018). These studies demonstrate that relatively modest RANS/URANS models continue to be suitable for supporting effectively experimental methods and are still the preferred choice in the industrial sector, even after the recent attention surrounding more sophisticated numerical methods, such as LES or DNS. In terms of the application of compound heat transfer enhancement structures, Shen et al. (2015) assessed the effect of rib-dimple and rib-protrusion turbulators under rotating conditions. The rib-protrusion geometry exhibited the best heat transfer rates for a reasonable pressure loss penalty, reaching the highest thermal performance for all considered rotation numbers. Nevertheless, this investigation was limited to a purely numerical study.
The key aims of this paper are to describe and quantify the changes in the local heat transfer of a ribbed leading edge with a rib-protrusion cooling feature in the second passage (enhanced) and to compare it with the ribbed channel (baseline). Particularly, we seek to clarify the impact of rotation on heat transfer rates for the enhanced design, which, according to published research, promises a remarkable improvement in the cooling effect. To this end, we apply the transient TLC technique and complement it with CFD results from a RANS model, which is validated here.
Experimental approach
Conducting heat transfer experiments for internal flows under engine-similar rotating conditions is a challenging task, particularly considering the need to capture local effects. Such effects are inherent to the geometry and operating point and can only be acquired via specific measurement techniques. In the following sections, the most relevant aspects about the rotating test rig, the test models, and the experimental heat transfer evaluation are examined.
Rotating test rig
In Figure 1 an overview with the key components of the test rig, which was presented in detail in Waidmann (2020), is shown. In an effort to correctly reproduce the buoyancy effects from the real machine, transient TLC experiments are performed with test air below the ambient temperature. Fluid temperatures as low as −100°C can be achieved for the three air supplies (precool air, tempering air and test air) by means of a heat exchanger operated with liquid nitrogen. Prior to the start of the experiment, precool air (1) is driven through the rotary union at the right hand-side of Figure 1 and flows through the pipes in the hollow shaft and rotor arm. These act as a heat exchanger to the test air pipes, which need to be precooled to a certain temperature so as to minimise heat intake during the experiment, thus facilitating the fluid temperature step change. Tempering air (2) with a temperature equal to the measured test model temperature is directed through the rotary union at the left-hand side of the figure. It continuously flows through the test model in order to pressurise it and to hold constant its initial temperature level. When the rotor pipes reach the desired temperature and the model is pressurised, the electric motor drives the shaft through a belt drive at a speed of up to 900 rpm. Once the target rotating speed, pressure level and test air temperature are reached, the test air (3) is driven through the test model, marking the start of the TLC experiment. This is achieved through a bypass valve unit consisting of six valves which enables the switch between the tempering air and the test air supply. The test air finally exits the shaft through the same rotary union.
The test bench was designed to enable the accurate setting of the target operating conditions. For this investigation, test cases are classified according to their Reynolds number (Re) and rotation number (Ro). The Reynolds number, determined as
Table 1.
Operating conditions and dimensionless parameters for the present investigation.
Test models
Baseline geometry
The baseline design has been derived from a previous work on a non-rotating test bench (Waidmann et al., 2013). The test model is made of acrylic glass in order to facilitate the optical access with cameras from the outside, and consists of two half-shells, a divider web and a tip wall. The inner channel walls are coated with TLCs and black backing paint. The geometry is comprised of a first passage (Pass 1) with a radially outward flow, a 180°-bend, and a second passage (Pass 2) with a radially inward flow. The first passage features a trapezoidal cross-section with a hydraulic diameter of
Enhanced geometry
The enhanced design, illustrated schematically in Figure 2 (left) and with the two half-shells (right), features the same rib configuration for PS and SS as the baseline design. In an effort to improve the heat transfer in the first passage, ribs from both channel sides are extended to the leading edge (LE) with a decreasing height, resulting in a triangular shape. In the second passage, the segments (i.e., the channel wall between two consecutive ribs) of PS and SS are equipped with a pattern of 3 × 3 spherical protrusions and a height-to-diameter ratio of
Experimental heat transfer evaluation
The experimental method is based on the transient TLC technique, as described in Poser et al. (2007, 2005) and Ireland and Jones (2000). By means of this approach, TLCs are used as temperature sensors and their response times, i.e., indication times, are determined after a sudden fluid temperature change is applied. Through analysis of the pixel-wise TLC indication times and the fluid temperatures, local heat transfer coefficients can be calculated. In the present investigation the TLC type G0C1W with a bandwidth of 1 K from Hallcrest has been applied and calibrated with the stationary calibration method proposed in Poser and von Wolfersdorf (2010), resulting in the indication temperatures presented in Table 1 for the baseline and enhanced geometries.
Heat transfer analysis is performed by means of the in-house code ProTeIn. The first steps involve wavelet-based filtering and adaptive normalisation, as presented in Poser et al. (2009). Following, the time at which the intensity of the green colour channel reaches its maximum, i.e., the TLC indication time, is determined for each pixel separately. The fluid temperature history for each channel position is determined by means of the CFD-based method presented in Gutiérrez de Arcos et al. (2022). The heat transfer coefficient h is calculated through solution of the one-dimensional Fourier heat conduction equation for a semi-infinite solid body and convective boundary condition. However, in order to approximate the actual fluid temperature history, this needs to be discretised through tiny temperature steps
The wall temperature corresponds to the temperature at the time of indication
Numerical setup
A numerical model implemented in ANSYS CFX 2021 R2 simulates the convective heat transfer in the fluid domain and supports the experimental approach where no data is available. This is the case for the leading edge of the baseline geometry, where optical access was not possible. Whereas the heat transfer experiments are of a transient nature, steady-state CFD computations have been performed. The setup has been successfully applied in previous investigations and allowed for accurate heat transfer predictions of the baseline cooling channel, as shown by Gutiérrez de Arcos et al. (2022), and in the qualitatively similar internal cooling channel under rotation presented in Göhring et al. (2018). The method is based upon the solution of the stationary Reynolds-averaged Navier-Stokes (RANS) equations in their total enthalpy form with the two-equation SST scheme by Menter (1994). Additional correction terms for the well-known delayed flow separation under adverse pressure gradients (reattachment modification) and insensitivity to streamline curvature and rotation (curvature correction) are presented in ANSYS CFX Theory guide (2021), and are applied here. The mentioned corrections have been validated in Göhring et al. (2016) and are used here due to their robustness and proven good comparability with experimental results. Air is modelled as an ideal gas and the transport properties viscosity and thermal conductivity are calculated by means of the Sutherland's equations (White and Majdalani, 2006). Regarding convergence, maximum residuals in the momentum and energy equations of
Boundary conditions
In Figure 3 an overview of the numerical domain with the applied boundary conditions is presented for the enhanced geometry exemplary. Fully developed flow conditions are present at the inlet. The three components of the velocity vector in Cartesian coordinates (X, Y, Z) are derived from a preceding calculation. Furthermore, the inlet temperature stems from the transient TLC experiment as an estimation of the average temperature for the duration of the experiment at the channel inlet, i.e., at the measurement location of the thermocouple pair TC0102. The outlet is characterised with a static pressure boundary condition equal to
Mesh generation and mesh independence study
The numerical grids were generated in ANSYS ICEM 17.1 (baseline geometry) and ANSYS ICEM 2021 R2 (enhanced geometry) following a multi-block structured approach. The different channel regions were modelled separately in order to allow for a better control of the desired target quality parameters, such as aspect ratio, grid angle and volume change, in accordance with the ANSYS ICEM CFD User’s manual (2021), and dimensionless distance of the first cell adjacent to the wall. In regard to heat transfer, high quality meshes with well-resolved near-wall regions are required. The dimensionless wall distance must not exceed
On the basis of the aforementioned constraints, a mesh independence study was conducted for the enhanced geometry, following the method proposed in Celik et al. (2008). Through this approach, the Grid Convergence Index (GCI), initially introduced by Roache (1994), is calculated and delivers an estimation for the grid discretisation error of a desired target variable. Three different grids (fine, medium, coarse) with a refinement factor of at least
Numerical heat transfer evaluation
Convective cooling is quantified by means of the heat transfer coefficient calculated with Newton's law (Incropera et al., 2017) with
and is made dimensionless with the Nusselt number. In Equation 2 the wall temperature
Results and discussion
In the following sections, heat transfer results are presented as the ratio of the local Nusselt number to the corresponding Nusselt number from the Dittus-Boelter/McAdams correlation (Williams, 2011) for fully developed turbulent pipe flow,
CFD validation
Experimental (EXP) and numerical (CFD) local heat transfer rates are depicted in Figure 4 and have been obtained for the baseline geometry with and without rotation, i.e., at
Figure 4.
Experimental and numerical heat transfer structure (a–d) and segment-averaged heat transfer (e and f) for the baseline geometry under rotation ( R o ≈ 0.15 ) and without rotation.
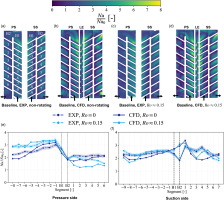
The non-rotating case, displayed in Figure 4a and b, features a heat transfer level that appears to increase towards the bend for the three considered channel regions. From inlet towards bend, a flow pattern consisting of detachment and reattachment to the wall caused by the angled ribs is repeated, as it can be appreciated from both, experimental and numerical results. Moreover, the trapezoidal shape of the first passage translates into generally higher heat transfer for PS than for SS. Directly downstream of the bend, a streak with high heat transfer rates is visible at the first segment of SS as a result of the 180°-turn, which triggers the cooling air impingement onto the SS wall. This structure is visible for both experiment and CFD simulation, however, in the experimental results the streak appears to be weaker in terms of heat transfer level. With disregard to the later point, the second passage is characterised by a monotonous heat transfer structure for PS and SS, and experimental and CFD results align qualitatively well.
As the cooling channel is set under rotation additional sources of momentum arise, altering the secondary flow field and ultimately impacting on the local heat transfer structure. In Figure 4c and d contour plots of the local heat transfer under rotating conditions
Regarding the enhanced geometry, experimental data for LE is available and can be therefore compared directly with the CFD results in Figure 5 for the rotating case
Rotationally-induced heat transfer
The integration of leading edge ribs and protrusions in the second passage is expected to alter the secondary flow field and thereby result in heat transfer enhancement. In Figure 6d and e, local heat transfer is depicted in form of
Figure 6.
Experimental heat transfer structure for the baseline (top) and enhanced geometries (bottom) under rotation (Ro ≈ 0.15) and without rotation. LE data for the baseline case stems from the CFD. (a) Baseline, non-rotating (b) Baseline, Ro ≈ 0.15 (c) Baseline, Ro ≈ 0.15 (d) Enhanced, non-rotating (e) Enhanced, Ro ≈ 0.15 (f) Enhanced, Ro ≈ 0.15.
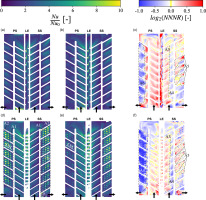
Under the presence of rotation the resemblance between PS and SS in the second passage of the enhanced geometry vanishes. Heat transfer rates remain high for SS, whereas they decrease drastically for PS. This is triggered by the governing Coriolis force direction, which deflects the cooling air from PS towards SS for the radially inward flow. The effect manifests itself in the secondary flow field visualisation from Figure 7, where in-plane velocity vectors in the PS near-wall region over the protrusions are depicted. The corresponding cross-sectional location (CS1) is indicated with a white line in Figure 6d and 6e. Additionally, the wall-perpendicular velocity component vy has been normalised with the average velocity of the plane (same value for rotating and non-rotating cases) and is displayed as contour plot. The sign, e.g. positive for air flowing towards the protrusions at SS, and magnitude of the vertical velocity component are revealed through application of a divergent colour legend. In the rotating case, the velocity vectors show considerably lower near-wall velocity gradients than in the non-rotating case. Furthermore, in the presence of rotation the Coriolis force lifts the air from the wall, directing to towards the opposite side (SS) and contributing to a reduced heat transfer level at the PS. A similar effect can be assumed for the baseline geometry. The rotational effect can be more clearly visualised through the use of the normalised Nusselt number ratio with a logarithmic scale to the basis of 2. Thereby, the enhancing and diminishing effect of rotation on heat transfer is revealed. In Figure 6c and f contour plots of log2(NNNR) for the baseline and enhanced geometries, respectively, are depicted. Rotationally-induced heat transfer enhancement is displayed in red; and rotationally-induced heat transfer decrease is displayed in blue. Yellow areas indicate little to no sensitivity to rotation. Whereas variation in the local heat transfer level and structure due to rotation between both geometries for SS is very limited (see A3, A4 and A5), the second passage of PS experiences a remarkable heat transfer decrease (A6), which is in agreement with the lower near-wall velocities noted previously for the rotating case. Furthermore, the rib-protrusion compound of the enhanced geometry intensifies this negative effect, as revealed by the contour plots. Considering the first passage of PS, a lower dependency on rotation exists for the enhanced geometry, as evidenced by the milder rotationally-induced heat transfer pattern. Focusing on the LE of the baseline geometry, a stream of increased heat transfer due to rotation develops from inlet towards bend, with the highest rotationally-caused increase at the channel inlet. The local structure changes completely for the enhanced geometry, where segment-wise zigzag-shaped streaks of increased heat transfer from inlet to bend are observed, with an overall milder rotational effect, compared with the baseline case.
Figure 7.
Detailed view CS1 (see Figure 6d and e) of the secondary flow field structure in the PS near-wall region for the enhanced geometry. (a) Non-rotating (b) Ro ≈ 0.15.
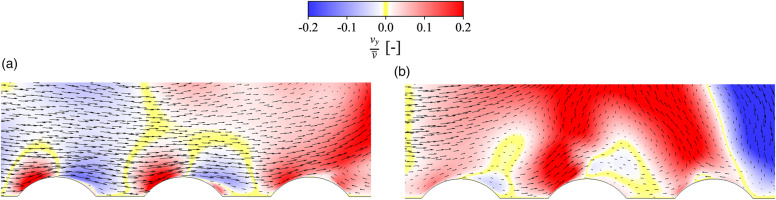
Summary and conclusions
This paper demonstrates the potential benefits of LE ribs and protrusions in combination with angled ribs for turbine blade internal cooling. First, a numerical model based on stationary CFD simulations is validated against transient TLC experimental data, exhibiting a noteworthy agreement. Hence, the model qualifies for supporting the experiment at the LE of the baseline cooling channel, where no experimental data could be obtained. A qualitative assessment of heat transfer data through contour plots reveals the changes in the local heat transfer structure with the incorporation of the additional turbulators. This alteration results in an overall higher heat transfer level under both rotating and non-rotating conditions, compared with the baseline geometry, i.e., ribbed channel. The examination of the presented data leads to the following key conclusions:
Under non-rotating conditions, a remarkable local heat transfer enhancement is evident at the location of the protrusions for PS and SS, with an overall higher heat transfer level than in the baseline case.
Under rotating conditions, the local heat transfer enhancement at the location of the protrusions for PS was marginal compared with the baseline geometry. Contrarily, the heat transfer level increased significantly for the protrusions at SS.
Under both non-rotating and rotating conditions, the integration of LE ribs as an extension of PS and SS ribs implies a beneficial effect on the heat transfer at the LE area, though it is not quantified here.
The isolated impact of rotation on heat transfer ranged from a slightly positive effect (PS first passage) to a substantially negative effect (PS second passage) in terms of heat transfer augmentation for the enhanced geometry. The secondary flow field visualisations from the CFD supported the heat transfer results and unveiled the reduction of near-wall velocities for the second passage of PS in the presence of rotation. Compared with the baseline geometry, the overall gain through rotation decreased, especially for the second passage of PS. Little variation was observed for SS.
Nomenclature
Latin symbols
cP
Specific heat capacity at constant pressure
Protrusion diameter
Hydraulic diameter
Heat transfer coefficient
Thermal conductivity
Mass flow rate
Rotational speed
NNNR
Normalised Nusselt Number Ratio (–)
Nusselt number (–)
Nusselt number from Dittus-Boelter correlation (–)
Pressure
Prandtl number (–)
Mean model radius
Reynolds number (–)
Rotation number (–)
Time
Temperature
Dimensionless wall distance of the first node (–)