Introduction
Mitigation of the adverse environmental impact of civil aviation constitutes a major objective for manufacturers, operators and regulatory and advisory bodies (Darecki et al., 2011; Scherer, 2019). According to the 20-Year Air Passenger Forecast of the International Air Transport Association (IATA), the foreseen 3.5% compound annual growth rate will lead to a doubling in passenger numbers compared to today’s levels (IATA, 2019). Responding to this demand, a series of revolutionary propulsion system architectures has been proposed to address the challenging future requirements (Epstein, 2014; Pornet & Isikveren, 2015; Bowman et al., 2018; Sahoo et al., 2020).
Electrified propulsion has emerged as a promising concept for enhanced fuel efficiency, reduced gaseous emissions and improved operability. The potential impact of hybrid electric propulsion in regional aviation was assessed for entry-into-service (EIS) technology of 2035 (Pornet et al., 2014). Block fuel reduction of up to 20% was achieved for a hybrid electric twin-engine narrow-body aircraft, with a single electric propulsor operated in cruise. However, this figure did not account for the life-cycle energy production requirements. Similarly, weight penalties eliminated performance improvements of turbo-electric aircraft featuring a boundary layer ingesting propulsor at the fuselage aft-end (Giannakakis et al., 2019). A more conservative, boosted concept was proposed for an 150-pax aircraft with a low-speed-shaft-coupled electric motor to provide power during take-off (Zhao et al., 2019a). Despite operability improvements, there was no significant fuel saving with 2035 technology levels assumed for all electrical components.
NASA reported 6–14% reductions in direct operating cost (DOC) for an 150-pax high-span hybrid electric aircraft relative to a non-electrified reference (Bradley and Droney, 2015). Nevertheless, these benefits were outperformed when costs associated with increased aircraft weight and complexity were included. The importance of charging the batteries with electricity from renewables to achieve concurrent reductions in CO2 emissions and DOC was highlighted for regional hybrid electric aircraft (Hoelzen et al., 2018). However, shifting to renewable energy ground-based plants includes complex considerations (Epstein and O’Flarity, 2019): airline operations are not evenly distributed around the globe and considerable transmission losses would occur unless renewable sources were installed around airports. Nevertheless, the area requirements and cost of infrastructure for installation of renewables near airports would be excessive.
The potential impacts of electrification on pollutant emissions are frequently outperformed by the associated weight penalties. Besides hybridization, low-emissions combustor technologies have been proposed to directly mitigate the environmental impact at source. Traditional rich-burn quick-quench lean-burn (RQL) combustion is initiated by a fuel-rich primary zone mixture, which yields combustor stability and low flame temperature, hence low NOx emissions. Next, a large portion of the dilution air is directed into the quick quench section to sustain a low equivalence ratio. Finally, the lean burn section is sized for the designated combustor outlet temperature. Lean direct injection (LDI) is a lean-burn combustion concept, where fuel is directly injected into the combustion chamber and quickly mixed with a large portion of air. Therefore, LDI can achieve reduced peak flame temperatures at medium to high power compared to traditional RQL combustors (Dewanji and Rao, 2015). However, LDI is more sensitive to combustion instabilities due to the challenging uniformity requirements in the fuel-air mixture before the reaction (Liu et al., 2017). This renders LDI performance largely dependent on the primary zone flame temperature ratio between take-off and cruise (Kyprianidis and Dahlquist, 2017).
The design of the primary zone of LDI combustors in terms of reducing carbon monoxide (CO) and nitrogen oxide (NOx) emissions, is governed by the trade-off between take-off and cruise emissions. These two operating conditions impose conflicting combustor design objectives, due to the diversity in the associated engine performance parameters which govern the primary zone flame temperature. Reduction of the lapse rate between take-off and cruise conditions was studied for intercooled recuperated configurations, featuring variable geometry low-pressure turbines (Kyprianidis et al., 2011). It was shown that a 60 K increase in the intercooled recuperated core temperature during cruise yielded 10% improvements in the landing and take-off (LTO) NOx margin relative to ICAO certification limits, due to the primary zone design balance between take-off and cruise conditions. Alternative methods to achieve reduced lapse rates involve de-rated thrust take-off procedures in excess runway length conditions (Takahashi, 2015).
The scope of this work is to re-evaluate LDI combustor capabilities towards “unlocking” the potential of electrification with respect to environmental impact and economic viability of medium-large aircraft propulsion. A geared turbofan configuration is employed, boosted by a battery-powered electric motor, coupled with the low-speed shaft of the gas turbine engine. The motor provides electric power during take-off, climb-out and climb to reduce the take-off-to-cruise turbine entry temperature (TET), therefore enhancing the effectiveness of LDI combustion. A multi-disciplinary design space exploration is carried out to assess the impact of different degrees of electrification. A specific hybridization strategy is proposed where the battery system is fully re-charged during descent yielding minimal ground infrastructure requirements and advancing the technology readiness level (TRL) of the proposed concept.
Methodology
Gas turbine engine simulation environment
The multi-disciplinary conceptual design and performance simulation framework EVA (Kyprianidis et al., 2008; Kyprianidis, 2017) is employed for the techno-economic and environmental gas turbine assessment undertaken in this work. EVA comprises a series of state-of-the-art individual modelling methods for multi-point gas turbine engine design, sizing and performance, mission simulation and economic analysis (Kyprianidis, 2019). The individual modules have been extensively described and validated (Kyprianidis, 2017) therefore further elaboration will be limited.
Combustor pollutant emissions are modelled based on validated correlations derived from experimental data (Kyprianidis and Dahlquist, 2017). RQL combustor NOx emissions index is expressed as function of combustor entry temperature and pressure, ambient humidity and combustor outlet-inlet total temperature difference. The LDI combustor NOx correlation is a function of combustor flame temperature and inlet total pressure. A pressure correction exponent factor of 0.5 is employed in the LDI combustor model, which is considered as conservative design choice (Kyprianidis and Dahlquist., 2017). The complete set of semi-empirical model parameters for RQL and LDI combustors is provided in the same reference, therefore restatement would be redundant.
The evaluation of direct operating cost is implemented through a cost break-down method (Jenkinson et al., 1999; Pascovici, 2008) based on real aircraft date. The major cost components under consideration are: (i) standing charges arising from depreciation, interest and insurance, (ii) crew cost, (iii) airport charges, (iv) cost of fuel and environmental taxes, and (v) maintenance cost for the airframe and the engine. The calculation of DOC is treated in a probabilistic manner, through consideration of major sources of uncertainty in the cost estimation input parameters. Therefore, the uncertainty associated with DOC calculation is quantified.
A multi-point engine design and performance simulation scheme performs a thermodynamic cycle matching at multiple operating points (Kyprianidis, 2010). A set of independent parameters (synthesis variables) is iterated at designated reference conditions to satisfy an equally-sized set of performance targets (synthesis targets) at specific operating conditions (Sielemann et al., 2020). Engine weight variations due to the multi-point synthesis procedure are considered negligible in the context of this work. A rubberized wing aircraft model is utilized for sizing the aircraft at fixed wing loading based on the designated mission range and propulsion system design. The basic principles of aircraft weight estimation, sizing, aerodynamics and performance are discussed in the relevant literature (Roskam, 1985; ESDU, 1997; Jenkinson et al., 1999; Torenbeek, 2013). Mission simulation is accomplished through an iterative method with total mission fuel convergence termination criterion (Kyprianidis, 2017).
Hybrid-electric configuration
A non-electrified, two-and-a-half-shaft geared turbofan engine configuration with 2035 EIS year technology assumptions (Sahoo et al., 2019; Zhao et al., 2019a) is employed as baseline engine for the purposes of this study. As previously mentioned, a multi-point synthesis method is used for gas turbine engine design and steady-state performance, where synthesis variables at hot-day top-of-climb (TOC) are varied to achieve the synthesis targets at hot-day end-of-runway take-off (EOR T/O) and mid-cruise operating conditions. Table 1 outlines the multi-point matching scheme selected for this engine architecture. The selection of optimal engine design parameters for minimum block mission fuel consumption has been undertaken for four key design synthesis targets, namely cruise overall pressure ratio (OPR), specific thrust (SFN), ideal jet velocity ratio (VcoldQhot) and pressure ratio split exponent (PRn) at cruise (Zhao et al., 2019a). Table 1 provides the optimized values of main design parameters for the baseline configuration.
Table 1.
Overview of multi-point synthesis scheme.
Single-aisle commercial airliners represent about 36% of the total aviation fuel consumption (Epstein and O’Flarity, 2019), therefore an 150-pax aircraft is employed to illustrate the potential impact of the present study. A benchmark flight profile with realistic mission phases is deployed (Zhao et al., 2019b). A range of 973 km is selected for the business case considered in this work, representative of typical short-medium range commercial aircraft operations. The aircraft is sized for a design range of 4,800 km, representative of this type of aircraft.
The electrified variant of this engine is implemented through coupling of a battery-powered electric motor with the low-speed shaft of the gas turbine. The electric motor provides electric power to the low-speed shaft during the ascending phase of the mission, which comprises the take-off, climb-out and climb stages. The aim of boosting is to off-load the low-pressure system during high-power conditions, therefore reducing the take-off-to-cruise TET ratio and consequently, CO2 and NOx emissions. During descent, an appropriate amount of power is extracted from the low-speed shaft to re-charge the batteries. The purpose of re-charging is to reduce compressor handling bleeds, but also to minimize new ground infrastructure requirements and accelerate the advancement of TRL of this concept.
Design space exploration framework
A multi-disciplinary design space exploration (DSE) strategy is implemented to investigate the impact of electrification on the environmental and economic potential of propulsion systems featuring conventional and lean-burn combustion technologies. The design variables considered in this investigation are the electric power input or extraction during the ascending and during the descending phase of the mission. The effects of simultaneous variation of these values is quantified with respect to total mission CO2 and NOx emissions, and DOC. A Monte Carlo simulation scheme is established to quantify the impact of uncertainty in key economic parameters on the calculation of DOC. The individual weight of the electrical power system components is approximated based on performance correlations and technology factors, therefore accounting for the primary effects of electrification on the overall aircraft weight. An overview of the design space exploration algorithm is illustrated in Figure 1.
The output of DSE is the overall system environmental and economic sensitivity to combined variations of the ascent and descent electrification scenarios. Optimized hybrid electric designs are identified achieving minimum CO2 and NOx emissions, whilst satisfying a set of surge-margin and net-electric-energy constraints at mission level.
Results and discussion
Gas turbine performance and operability
The impact of combined variation of ascending and descending electric power input or extraction on the ratio of TET between take-off and cruise is illustrated in Figure 2a. Each and every point of the DSE representation corresponds to a dedicated gas turbine multi-point design synthesis, electrical power system weight estimation, aircraft sizing and full mission simulation. The analysis has been undertaken at energy level to illustrate the relative requirements between ascent and descent. Positive sign represents electric power input, whilst negative corresponds to power extraction. The baseline, non-electrified, turbofan configuration will serve as reference point for the analysis to follow. Furthermore, the line of zero net electric energy between ascent and descent describes the locus of electrified propulsion designs beyond which no ground charging or replacement of batteries is required. Overall, the TET ratio between take-off and cruise is primarily governed by variations of the ascent electric energy input. Boosting the low speed shaft in high power conditions leads to lower OPR and HPC delivery temperatures, hence reduced TET during ascent (Walsh and Fletcher, 2004). The baseline TET ratio of 1.22 between take-off and cruise can drop down to 1.12 for relatively high degrees of ascending power hybridization.
Figure 2.
Impact of electrification on gas turbine performance as function of electric energy input to the low-speed shaft during ascent and descent of 973 km business case; (a) take-off-to-cruise TET ratio, (b) IPC surge margins in descent and top-of-climb.
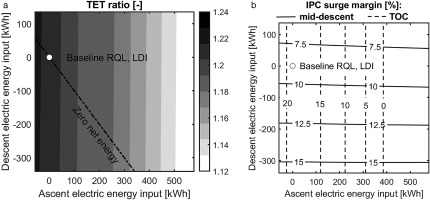
Electric power input or extraction has impact on the operability of gas turbine components. Operability is represented by surge margins, defined at constant rotational speed line, as the pressure ratio (PR) difference between the surge line and the off-design point divided by the surge line PR (Kavvalos et al., 2019). For the specific concept under investigation, it has been shown that at the top of climb (TOC), it is the surge margin of the intermediate pressure compressor (IPC) which is more sensitive to dropping below acceptable thresholds, since boosting leads to a rise in IPC PR and reduction in mass flow (Zhao et al., 2019a). Since the engine thrust levels remain fixed, the rotational speed of the LP shaft will remain nearly unaffected. That unavoidably gives rise to a mass flow miss-match between the LP and HP shaft. To balance this miss-match, the mass flow and PR of the IPC are reduced, which directs the operating point of this component closer to surge. The same component represents the “bottleneck” in mid-descent. Figure 2b shows the impact of electrification on the operability of the most critical gas turbine component during ascent and descent. Excessively high boosting during ascent can lead to negative surge margins, whilst power extraction from the low-speed shaft during descent improves operability through reducing compressor handling bleeds (Kurzke and Halliwell, 2018). For the purposes of this investigation, a 10% surge margin will be considered as lowest operability threshold, therefore defining the constraints for the search of optimal hybrid electric configurations across the designated design space.
NOx emissions
Figure 3 presents the break-down of NOx emissions along the benchmark business-case profile for a gas turbine engine featuring RQL and LDI combustor. No electrification strategy is considered in this comparison. The vertical axis is normalized based on the total NOx emitted for the RQL case. It is shown that total NOx emissions for the LDI combustor are 32% lower compared to the RQL, in accordance with the findings quoted in previous studies (Forum-AE, 2015). For the RQL combustor, 70% of the total mission NOx is emitted during the ascending phase of the mission which comprises take-off, climb-out and climb. The same figure for the LDI combustor reaches 78%, which highlights the importance of reducing take-off-to-cruise TET ratio in this configuration through boosting. It is worth noting that for the 973 km business case, the duration of the descending phase is about 2.4 times larger than the ascending one, which allows for a lower degree of power hybridization during re-charging, therefore keeping IPC descent surge margins at acceptable levels.
Figure 4a illustrates the effects of electrification on total mission NOx for RQL combustors. The results are normalized based on the total emissions of the non-electrified baseline configuration. Electrified designs laying above and right of the zero-net-energy line offer flight NOx deltas of up to −8.5%, however without resolving the additional emissions associated with ground battery charging. The aim of this study is to propose a hybrid electric design with minimal ground charging requirements, therefore, the search space for the optimal configuration reduces to the locus of zero net electric energy designs. Furthermore, the 10% surge margins are superimposed, effectively defining the design constraints for this configuration. Consequently, the optimal electrified design requires 220 kWh of electric energy input during ascent, which is entirely recovered during descent. This is translated to a 9.5% degree of power hybridization during ascent and −6.2% during descent, based on the associated duration of each mission phase.
Figure 4.
Impact of electrification on NOx emissions as function of electric energy input to the low-speed shaft during ascent and descent of 973 km business case; (a) RQL combustor, (b) LDI combustor.
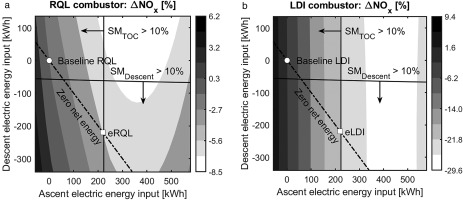
NOx is primarily governed by variation in electric energy input during ascent, due to the impact of low-speed-shaft off-loading on TET. Nevertheless, power extraction during descent has also an effect on total NOx. For the set optimization constraints, the optimal electrified RQL configuration (eRQL) demonstrates −4% NOx deltas relative to the baseline RQL. The associated TET ratio between take-off and cruise is 1.18, which is 2.5% lower than the baseline. For a combination of 14.7% ascent and 6.2% descent hybridization, a total NOx delta of −7.7% occurs; albeit at a cost of ground emissions and infrastructure requirements for battery re-charging or replacement. Of course, these figures would be altered if renewable energy sources were considered, but this is beyond the scope of the present work. It is worth noting that if electrical power system weight had been neglected, NOx deltas between eRQL and baseline RQL would be −6.2%, which depicts the importance of including the first-order effects of electrification on aircraft weight estimation (Perullo et al., 2016).
Figure 4b presents the corresponding response for LDI combustors. It is observed that total mission NOx is less sensitive to power input or extraction in low-power descent conditions. The benefits of electrification present considerably higher margins compared to the corresponding RQL figures. Specifically, a NOx delta of −19.8% is calculated for the optimal hybrid-electric engine with LDI combustor (eLDI) relative to the non-electrified LDI variant. As discussed in Figure 3, LDI technology alone results to NOx reductions in the order of 32%, yielding a cumulative NOx saving in the order of 46% for the eLDI configuration, relative to the non-electrified RQL. It is therefore demonstrated that electrification presents better potential for application on engines featuring LDI combustors, roughly promising a halving of total NOx emissions with respect to their non-electrified RQL counterparts.
CO2 emissions, economics and uncertainty
The effects of low-speed shaft power input or extraction during ascent and descent are essentially reflected on the total mission CO2 emissions, as shown in Figure 5a. It is noted that the gas turbine performance model does not account for variations in the combustor configuration, therefore the present CO2 analysis represents both RQL and LDI variants. The CO2 delta corresponding to the NOx-optimized electrification strategy is 0.5% relative to the baseline engine. It is noted that a separate optimization for CO2 along the zero-net-energy line would yield a 0.1% delta. The best attainable CO2 delta in flight is −3.3%, however it is expected that this number would be penalized by CO2 emissions associated with ground battery charging or replacement. Designs below the zero net energy line present increasingly positive CO2 deltas due to unnecessary charging in flight. The previous considerations depict that there is significant CO2 benefit expected from the optimization of this configuration. Nevertheless, it is the potential reduction of NOx emissions that shall be the motive for optimizing this concept, whilst keeping associated CO2 penalties at a minimum.
Figure 5.
Impact of electrification on CO2 emissions and economics as function of electric energy input to the low-speed shaft during ascent and descent of 973 km business case; (a) CO2, (b) direct operating cost.
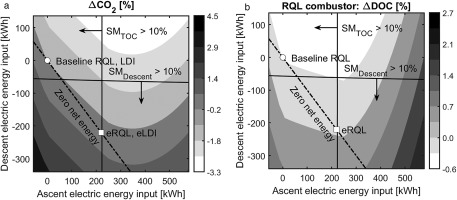
Variations in fuel consumption and pollutant emissions due to hybrid electric designs are essentially reflected on aircraft DOC. Estimation of DOC requires input from many market-related parameters which fluctuate with time. For this reason, a deterministic cost estimation is avoided and a probabilistic approach for the evaluation of DOC is developed. Specifically, a Monte Carlo simulation scheme is established to account for uncertainties in key economic parameters, namely fuel price, exchange rate, interest rate and inflation rate. The mean value and associated uncertainty for these parameters is calculated based on one-year-horizon historical data. The statistical analysis undertaken for the historical data suggest Gaussian distributions to be assigned to all uncertain input parameters.
The distribution of the mean value of DOC relative deltas for the engine equipped with RQL combustor is represented in Figure 5b. It is noted that each and every point of this illustration represents a dedicated Monte Carlo simulation with sample size of 1,000 points, which was found to be sufficient for the convergence of the first four statistical moments of DOC. It is observed that DOC follows similar patterns as CO2, hence fuel is the parameter which governs the response of DOC for this configuration. The corresponding distribution for the LDI configuration is almost identical, hence it was deemed unnecessary to include this illustration. For both RQL and LDI hybrid electric variants, mean DOC delta varies between –0.6% and 2.7% across the design space, whilst the optimal electrified designs present a delta of roughly 0.4%. It is concluded that the investigated hybrid electric concept does not offer significant DOC reductions, nor brings increased running costs.
The associated DOC variability is uniformly distributed throughout the design space, presenting a ±2.5% uncertainty within 95% confidence intervals. The quoted mean DOC deltas and associated uncertainty are based on one-year time windows. However, different time horizons shall be considered for the evaluation of economic viability of the proposed design. Table 2 presents the quantification of uncertainty within one-, five- and ten-year horizons, all referring to the optimized electrified design of the RQL variant within 95% confidence intervals. It is shown that the mean value of DOC delta is not significantly affected; however, the associated uncertainty can reach up to ±8.4% in a ten-year horizon. Almost identical numbers where accrued for the eLDI configuration which depicts the relatively low impact of the present NOx taxation rate on DOC.
Table 2.
Direct operating cost uncertainty analysis (95% confidence intervals) at different time horizons.
A variance-based Sobol sensitivity analysis (Sobol, 1993; Homma and Saltelli, 1996) is carried out to quantify the relative contribution of each uncertain input parameter to the overall system uncertainty. The calculated Sobol global sensitivity indices are uniformly distributed across the design space, therefore only the range of variation for each index is provided. Specifically, fuel price variations contribute 69–72% to the overall uncertainty, whilst interest rate is responsible for 25–29%. Uncertainties in the exchange and inflation rates get only 2–3% and 0–1% of the total share, respectively. The above numbers reveal which are the economic parameters that should be primarily examined in the evaluation of new concepts.
Impact of electrical power system technology
Sizing of the electrical power system is crucial for the realistic estimation of environmental and economic deltas for new concepts (Wroblewski and Ansell, 2019). In this work, the first-order effects of electrification on aircraft weight are captured via utilizing technology factors for the individual components (Pornet et al., 2014; Bradley and Droney, 2015; Gnadt et al., 2019; Zhao et al., 2019a). 2035 EIS technology levels have been assumed in the results presented in the previous sections. However, it is deemed necessary to investigate the impact of technological assumptions on the anticipated deltas. Therefore, two different time-frames are also considered, 2020 and 2050. Table 3 summarizes the technological assumptions considered for each component of the electrical power system.
Table 3.
Specification of electrical power system components at different time-frames.
Figure 6a presents the impact of electrical system technology levels on NOx deltas for optimized RQL and LDI hybrid electric configurations. For the RQL configuration, electrification benefits are outperformed by weight penalties imposed due to the relatively low battery specific energy in the 2020 time-frame, yielding a 7% increase in NOx emissions relative to their non-electrified counterparts. Similarly, as shown in Figure 6b, DOC and CO2 deltas are in the order of 3.5% and 5%, respectively, in 2020. In the 2035 and 2050 time-frames, electrified RQL configurations achieve 4% and 5% NOx reductions, whilst the corresponding figures for LDI are 19% and 20%. CO2 and DOC range between 2% and 0% for both combustion technologies, in 2035 and 2050. Overall, for the 2035+ time-frame, it is concluded that due to the relatively low degrees of power hybridization, the impact of electrical power system weight is small compared to more aggressively electrified configurations. This increases the level of trust to the proposed hybrid electric concept, which demonstrates adequate robustness for consideration in both mid- and long-term electrification solutions. It is noted that the accrued deltas are subject to the technological assumptions regarding electrical components and combustor performance. Nevertheless, this study aims to showcase the associated sensitivity magnitudes and provide insight about the technological maturity levels required to enable the utilization of these concepts.
Impact of fuel price and NOx taxation
The Sobol-based sensitivity analysis demonstrated that fuel price is the governing source of uncertainty in the probabilistic calculation of DOC. Fuel price does frequently exert extreme variations due to socio-geo-political events and circumstances. Furthermore, NOx taxation varies considerably around the globe, whilst much stricter future policies are anticipated in the context of suppressing LTO emissions. Therefore, the sensitivity of accrued DOC is explored in extreme variations of fuel price and NOx tax. Fuel price is varied between −80% and 80% and NOx tax between −50% and 500%. Table 4 summarizes the mean DOC deltas and associated uncertainties for both eRQL and eLDI variants, relative to their non-electrified counterparts. Mean values and corresponding uncertainties for the input economic parameters are based on one-year-horizon historical data.
Table 4.
Impact of fuel price and NOx tax on direct operating cost.
ΔDOC (%) | Fuel price −80% | Fuel price +80% | |
---|---|---|---|
NOx tax −50% | eRQL | 0.5 ± 1.5% | 0.4 ± 3.7% |
eLDI | 0.3 ± 1.5% | 0.3 ± 3.7% | |
NOx tax +500% | eRQL | 0.1 ± 1.3% | 0.1 ± 3.3% |
eLDI | −0.6 ± 1.3% | −0.5 ± 3.3% |
It is observed that for low fuel prices DOC uncertainty is around 1.3–1.5%, whilst high fuel prices yield uncertainties between 3.3–3.7%. On the other hand, high NOx tax reveals negative DOC deltas for the eLDI configuration. which highlights the potential economic benefits of the proposed technology, if stricter NOx taxation is applied. Overall, fuel price governs the uncertainty in DOC estimation, whilst a potentially higher future NOx tax would render the electrified LDI engine more economically attractive compared to traditional or electrified RQL configurations.
Impact of business case range
The simulation campaign discussed in the previous sections refers to a business case ranging 973 km. However, the aircraft is sized for a design range of 4,800 km through the rubberized design procedure described in the “Methodology” Section. It is noted that the practical assumption made for the batteries implies modular pack technology, allowing the employment of suitable battery size on-board, according to the mission requirements.
The relative deltas for the business case NOx emissions representing both electrified RQL and LDI configurations are depicted in Figure 7a and b, respectively, for 2035 technology assumptions. It is shown that due to the different NOx patterns between RQL and LDI configurations, different optima occur. Specifically, the NOx-optimized eRQL configuration is quite close to the baseline, yielding only −0.1% relative delta, whilst the eLDI figure is −10.4% relative to the non-electrified counterpart. It is observed that for the 4,800 km business case range, the anticipated mission NOx savings are considerably reduced compared to the 973 km range. In high business case ranges, increased fuel is required on board which yields longer ascent and descent times. However, the duration of the cruise segment is extensively increased, which results in a lower relative duration of the ascent and descent stages as parts of the complete mission. Therefore, the impact of electrification in ascent and descent is less pronounced when deltas refer to the complete trajectory emissions.
Figure 7.
Impact of electrification on NOx emissions as function of electric energy input to the low-speed shaft during ascent and descent of 4,800 km business case; (a) RQL combustor, (b) LDI combustor.
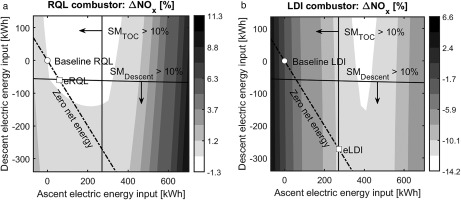
Figure 8a and b represent the distribution of RQL CO2 and DOC deltas for the same operational scenario. It is noted that the corresponding distributions for LDI configurations are almost identical, hence not included in the illustration. It is shown that the minima for both quantities coincides with the baseline non-electrified configuration on the zero net energy line. This is expected since the aircraft conceptual design is optimized for minimum block fuel in the design mission of 4,800 km. The CO2 deltas arising from the optimization with respect to NOx for RQL and LDI configurations are 0.2% and 1.1%, respectively. Similarly, the corresponding probabilistic DOC deltas are 0.1% and 0.8%.
Figure 8.
Impact of electrification on CO2 emissions and economics as function of electric energy input to the low-speed shaft during ascent and descent of 4,800 km business case; (a) CO2, (b) direct operating cost.
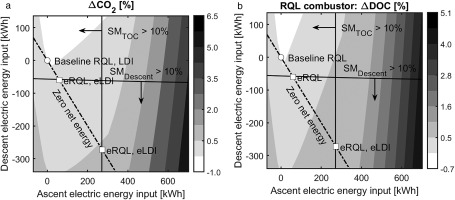
Table 5 provides a generalized quantification of the impact of business case range and time-frame on the anticipated benefits of electrified RQL turbofan configurations. Table 6 provides the corresponding figures for electrified LDI. It is noted that the complete set of simulations included in the DSE and optimization procedure has been conducted for the medium- and long-range scenarios under investigation. The environmental and economic deltas are mission-dependent and favorable for short-range operations. A linear correlation between mission range and accrued benefits is observed. Overall, it can be concluded that for short-range missions, technology levels of year 2035+ would be required for tangible NOx improvements through electrified LDI configurations. For long-range missions, improvements are considerably reduced, therefore depicting the limitations of the investigated technology.
Table 5.
Impact of business case range on the environmental and economic potential of electrified RQL configurations at different time-frames.
Table 6.
Impact of business case range on the environmental and economic potential of electrified LDI configurations at different time-frames.
Conclusions
A systematic design space exploration has been presented for the quantification of environmental and techno-economic potential of a hybrid electric turbofan configuration featuring lean direct injection combustor technology. It has been shown that boosting the low-speed shaft during the ascending phase of a benchmark mission leads to reduced take-off-to-cruise TET ratio which yields reduced NOx emissions. A battery-recharging strategy during descent has been introduced, rendering the aircraft independent of ground charging or additional infrastructure, therefore advancing the TRL levels of the proposed concept.
For traditional RQL combustor technologies in short-range business cases, electrification leads to 4% NOx reductions relative to the associated non-electrified variant. The corresponding improvement margins for electrified turbofans with LDI combustors rise to 19.8% relative to non-electrified LDI, showcasing the improved potential of this technology compared with RQL. Overall, optimized hybrid electric configurations with LDI combustor promise a 47% reduction relative to non-electrified RQL configurations, primarily attributed to the reduced lapse between take-off and cruise primary zone flame temperature which allows more balanced combustor designs. These benefits come at a 0.4% penalty in CO2 emissions and direct operating cost, demonstrating that added weight due to electrification outperforms theoretical fuel benefits. The anticipated environmental and economic deltas are linearly correlated with mission range. For the long-range design mission scenario, the corresponding NOx benefits for electrified LDI configurations drop to −10%, depicting the limitations of the proposed technology.
Potentially stricter NOx taxation policies are beneficial for LDI combustors, yielding the technology more economically viable compared to RQL. Finally, the impact of electrical power system technology on the anticipated deltas is relatively small in the 2035+ time-frame due to the low degrees of power hybridization required for the implementation of the proposed concept. This increases the level of confidence on this strategy, rendering the concept a robust technological solution for the mid- and long-term. Future studies can be focused on expanding the findings of this work, through alternative electrification architectures, or even non-electrified configurations, capable of reducing the lapse rate between take-off and cruise and mitigating the environmental impacts of future aviation.