Introduction
Industry aims to optimise gas-turbine engines to increase reliability and efficiency, while reducing pollutant and noise emissions to comply with more restrictive regulations. Nowadays, these engines are still designed following individual paths for each component (compressor, combustion chamber, turbine and others) by different departments of the same company. Each component is designed and manufactured individually and then assembled together. An important practical problem that could be encountered is that the resulting engine may exhibit overall poorer performance than the one obtained from the individual component optimisations due to integration effects, possibly requiring additional costly processes due to redesign of the latter. In the design process, Computational Fluid Dynamics (CFD) has been progressively adopted from two-dimensional simulations of blade profiles to a more accurate three-dimensional representation of a component. Simulations with the Reynolds-Averaged Navier-Stokes (RANS) method have been the industry's primarily choice, especially for the design of individual components since their computational cost is limited and results are acceptable at nominal conditions (Pinto et al., 2017). Today, as a result of the increase and easier accessibility to computing power, higher fidelity methods such as unsteady RANS (URANS) and Large-Eddy Simulations (LES) are gradually being used (Tucker, 2011a,b; Gicquel et al., 2012; Gourdain et al., 2014; Anand et al., 2021). However, their usage is still mainly limited to academic configurations, and when it is done for industrial engines, it is so to compute periodic sectors of individual components. In such cases, boundary conditions are usually defined either by imposing zero-dimensional single values (average quantities), one-dimensional profiles or steady two-dimensional contours on the inlet and outlet boundaries. These can be obtained from the performance cycle of the machine or inherited from the time-averaged solution of an adjacent component (e.g. the turbine stage inlet is inherited from the outlet of the combustion chamber). However, simulations of individual components do not share unsteady information such as turbulence intensity and velocity length scales that are approximated if imposed. As a result of these approximations, bidirectional unsteady interactions between components remain unavailable for simulations of single components. Note finally that ideally and for such compressible flows, acoustic treatments or acoustic impedances should also be prescribed at inlet or outlet since these parameters can greatly impact the stability map of a combustion chamber (Poinsot, 2013) for example or any CFD simulation.
In order to overcome some of the simplifications needed to define flow-boundary specifications of individual components, several attempts have been made to couple two components of the engine. In some works, RANS or LES solvers were used for the combustion chamber and URANS solvers for the turbine (Salvadori et al., 2012; Insinna et al., 2014; Jacobi et al., 2017). Nonetheless, these approaches still lead to strong hypotheses on the information provided from one code to the other, implying approximations on the mass-flow rate, total energy and turbulent quantities. Using a single LES solver to solve the full system constitutes a high potential solution to avoid these approximations (Duchaine et al., 2017; Miki et al., 2018; Thomas et al., 2019; Miki et al., 2020). Such multi-component LES simulations for example accurately represent the critical unsteady high temperature spots issued from the combustion chamber that impact on the turbine blades. An integrated simulation of a radial compressor and a combustion chamber (Pérez Arroyo et al., 2020) demonstrated that the pressure fluctuations generated by the interaction of the impeller with the radial diffuser reach the combustion chamber, potentially modifying the shape of the flame which could change the interaction with an eventual turbine stage.
The first attempt to simulate three components at once was performed by the Center for Turbulence Research at Stanford University (Schlüter et al., 2005; Medic et al., 2007a, b). Their strategy was to use an incompressible LES solver for the combustion chamber and a compressible URANS second solver for the compressor and turbine stages. From a scientific point of view it was a remarkable milestone, however, the methods and framework used to couple the codes were complex and as a result, the integrated simulation failed to produce meaningful results to the author's knowledge. Recently, a cost-efficient RANS-based simulation of the compressor, combustion chamber and turbine stage (Romagnosi et al., 2019) was performed using the Nonlinear Harmonic Method (He and Ning, 1998) to characterise unsteady phenomena. In this case, results are compared against a classical mixing plane approach that by nature, spatially averages variables, which accentuates the need for meaningful unsteady methods to transfer the information at the interfaces between components.
In the current work the first reactive LES of an integrated 360 degrees engine with three main components (fan, compressor and combustion chamber) is presented. The engine considered is the DGEN-380 (Price Induction, Inc. and Akira Technologies). The engine is relatively compact but contains many technological features of current turbofan engines (including combustion) and it is currently used as a demonstrator at NASA and ISAE-SUPAERO. These characteristics make it a good candidate to simulate numerically. However, being a rather new demonstrator, related research is scarce. The associated available literature found can be grouped in 4 categories: performance cycle studies using 0D approximations (Pilet et al., 2011; López de Vega et al., 2019), acoustics and liners research (Berton, 2016; Brown and Sutliff, 2018; Nark et al., 2018; Sutliff et al., 2019; Nagai et al., 2019) including combustion noise (Boyle et al., 2018, 2020), experimental and RANS campaigns at wind-milling conditions (Dufour et al., 2015;García Rosa et al., 2015; Dufour and Thollet, 2016) and experimental as well as LES investigations of the flow around the fan and the Outlet-Guide Vanes (OGV) at the nominal operating point (Odier et al., 2017, 2018).
This study is structured as follows. First, the configuration is introduced and the numerical setup is detailed. Secondly, the methodology to carry out the integrated simulation is explained and a special focus is made on mesh generation and High-Performance Computing (HPC). Thirdly, the initialisation and convergence of the 360 degrees domain is presented. Then, the flow topology of the transonic compressor is introduced. Finally, main conclusions are listed. Results are analysed in detail and compared against stand-alone LES predictions of each component in the companion paper (Pérez Arroyo et al., 2021).
Configuration and numerical setup
Configuration
As mentioned above, the configuration numerically studied corresponds to the DGEN-380 demonstrator and includes the full 360 azimuthal degrees of the fan stage, the compressor and the combustion chamber as a first attempt to simulate the full engine. Results are compared against stand-alone simulations of each component that are performed on a CFD-friendly azimuthal sector of 360/14 degrees for the fan and OGVs, 360/11 degrees for the compressor and 360/13 degrees the combustion chamber. This required the modification of the number of OGVs for the fan from 40 to 42 (Odier et al., 2018), and the number of radial and axial diffuser for the compressor from 19 to 22 and 57 to 55, respectively. The modification of the number of diffuser vanes is performed by increasing the height of the channel while keeping constant the total cross-sectional area to keep an equal mass-flow rate. Nevertheless, due to the small reduction of blade count, no modification of the angle of the radial vanes leading-edge is expected. RANS simulations for the real and modified geometry were performed for the compressor to verify that the operating point was not altered by the geometry simplification. The geometry of the 360 degrees simulation has been simplified according to these modifications in order to have a fair comparison with the stand-alone simulations. Likewise, other non-azimuthally periodic characteristics such as supporting struts or an added ignition fuel injector are not considered for the simulations. The fan stage contains a cylindrical inlet, 14 blades, 42 OGV and the bifurcation into the primary and secondary flows. The radial compressor is composed of 11 main blades and 11 splitter blades, as well as a radial and an axial diffusers composed of 22 and 55 vanes, respectively. The annular combustion chamber contains a contouring casing, the flame-tube and a straight outlet. The liners of the flame-tube include effusion-cooling, primary and dilution holes as well as a double contra-rotating swirler for each azimuthal sector.
The domains of the stand-alone simulations are illustrated in Figure 1a–1c and are detailed in the following. The domain for the fan and OGVs (noted as FAN + OGV) starts at the inlet of the engine and ends at the inlet of the impeller of the radial compressor, where the outlet has been axially extended to ease the evacuation of turbulence. For the secondary flow, it reaches the axial position of the exit of the real engine but no exterior domain has been considered. The domain for the compressor (denoted as CoHP) has a short straight inlet that leads to the impeller, followed by the radial and axial diffusers and exits as a straight annular duct of the same height as the one found on the axial diffusers. Last, the combustion chamber domain (hereafter referred as CC), has a straight inlet with no axial diffuser vanes and a straight outlet instead of the turbine stages. The diffuser vanes were not considered for the stand-alone simulation of the chamber because its azimuthal periodicity is different from the one for the chamber. In order to perform the full integrated simulation, first an intermediate 360 degrees computation including the compressor stage and the combustion chamber as depicted in Figure 1d was carried out (noted as CoHP + CC). Finally, the full integrated domain from the fan inlet to the combustion chamber outlet is shown in Figure 1e and related results will be referred to as FULLEST (First fUlL engine computation with Large Eddy SimulaTion).
Figure 1.
View of the domain for each simulation. Blue depicts the static sub-domains, and green and yellow the rotating sub-domains depending on its rotational speed. Lines and markers in Figure 1e are used as a reference throughout this work. (a) FAN + OGV domain (1 sector). (b) CoHP domain (1 sector). (c) CC domain (1 sector). (d) CoHP + CC (360°). (e) FULLEST (360°).
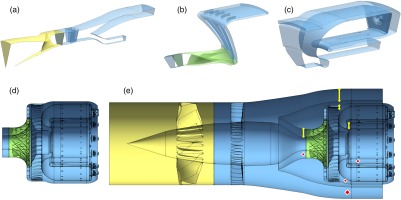
In this work, the operating point of study corresponds to take-off with opposite rotational speeds of 13,053 and 51,930 rpm for the fan and radial compressor, respectively. The total designed mass-flow rate is 13.846 kg/s with a by-pass ratio of 6.84. On the real engine, an effective suction of 1% of air is present within the compressor stage through a series of different outlets. In the present simulations this suction is mimicked at a position located on the compressor hub between the impeller and the radial diffuser. In order to ease the comparison against the design operating point, only the effective mass-flow rate after suction will therefore be considered (i.e. the mass-flow entering the combustion chamber). Last, the compressor works at a pressure ratio of 4.6 and the combustion chamber reaches temperatures of roughly 2,500 K and operates with a fuel to air mass-flow ratio of 0.018.
Numerical setup
The reactive as well as the non-reactive LES are performed with the code AVBP, the explicit unstructured and massively parallel compressible flow solver developed by CERFACS (Schönfeld and Rudgyard, 1999). All numerical predictions have been carried out using the explicit second-order scheme Lax-Wendroff (Lax and Wendroff, 1964) and the subgrid-scale model relies on the Wall-Adapting Local Eddy (WALE) viscosity model (Nicoud and Ducros, 1999). Note also that to reduce the computational cost of all simulations, a standard log-law is applied on all solid boundaries with slip conditions (Schmitt et al., 2007). This reduces the cost not only because the total number of cells is reduced but also because it increases the cell size at the wall and thus, the minimum time-step computed through a global Courant-Friedrich-Levy number is increased compared to a wall-resolved simulation. For combustion, the thickened-flame model (Colin et al., 2000) is used to account for combustion–turbulence interaction along with a reduced chemistry with 6 species and 2 reactions (Franzelli et al., 2010) where a purely gaseous premixed mixture is injected. In addition, the thickened-hole model (Bizzari et al., 2018) is introduced to represent the micro-perforations in the flame-tube. Non-reflective Navier-Stokes characteristic boundary conditions are used at inlet (Poinsot and Lele, 1992; Odier et al., 2019) and outlet (Granet et al., 2010; Koupper et al., 2015) without any kind of synthetic turbulence. This setup was shown to provide the best trade-off between accuracy and computational cost (Gicquel et al., 2012).
The variables specified as input parameters at inlet and outlet boundaries of the stand-alone simulations are the following. For the FAN + OGV, mass-flow rate and static temperature are defined at the inlet and static pressure at the outlets (different for the primary and secondary flows). The same approach is used for the CC domain whereas for the CoHP, total pressure and temperature are set at the inlet and static pressure at the outlet. The integrated simulation uses the same boundaries as the inlet of the FAN + OGV and the outlet of its secondary flow, along with the outlet of the combustion chamber.
When it applies, the transfer of the flow between the static and rotating sub-domains is performed with an overset grid method over a common geometrical zone for the proper exchange of the necessary information (Wang et al., 2014; de Laborderie et al., 2018). AVBP is based on the SPMD paradigm for parallelism (Single Program - Multiple Data). In the case of this simulation separate in-code instances are automatically generated for static and rotating sub-domains. Each instance is coupled internally using the CWIPI library from ONERA (Refloch et al., 2011; Duchaine et al., 2015). Since there are two different rotational speeds, the integrated simulation FULLEST utilises three instances of AVBP to run as illustrated by Figure 2: one for the static sub-domain, one for the fan sub-domain, and one for the impeller sub-domain. The different instances for the stand-alone simulations are colour-coded according to Figure 1.
Details concerning the mesh used for each simulation are provided in Table 1 along with the wall-clock time per physical millisecond for the given number of cores. All meshes are unstructured and solely made of tetrahedral elements. The FAN + OGV mesh is similar to the “M1” mesh computed by Odier et al. (2017) with
Table 1.
Details of the simulations.
Methodology and initialisation
Regardless of the ability of the codes to perform such extreme simulations, the major difficulty lies in a clever methodology of initialisation to save computational cost complemented by a strategy to yield the best trade-off to solve potential machine dependent memory and HPC limitations (e.g. partitioning). Although menial, these technical and often unavailable details are of paramount importance if one wants to reproduce such simulations. This section presents the methodology used to carry out the integrated simulation FULLEST. In particular, details about the stand-alone simulations are given followed by the approach used to generate the mesh consisting of over 2 billion cells and its associated initial solution, the mesh partitioning procedure, the initialisation and convergence of FULLEST as well as an initial comparison of the operating point between integrated and stand-alone simulations. In addition, the flow topology generated by the radial compressor working at transonic conditions is introduced.
Initialisation and convergence of the stand-alone simulations
Performing the simulations of the stand-alone components has three goals. First, a data-base for each component without any interaction with its surrounding is obtained at a reduced cost. Secondly, such a prediction can then be used as a reference for the integrated simulation. Thirdly, as proposed by Pérez Arroyo et al. (2020), the final (i.e. converged at the correct operating point) instantaneous flow snapshot is used as initial solution of each specific component to launch the integrated simulation. The simulations FAN + OGV were initialised from previous LES solutions provided by Odier et al. (2018), updating the rotational speed of the fan and inlet as well as the outlet boundary conditions. In that case, note that a short trial and error setting period to find a satisfactory static pressure at the outlet boundaries was necessary to ensure the correct bypass ratio. Once the transient finished, data was acquired during 10 fan rotations for flow analysis. Note that as of today, one brute force possibility to initialise compressor simulations is to start with the flow at rest and then increase progressively the rotational speed and outlet pressure as explained by Dombard et al. (2018). Using this approach, convergence would be achieved within 10 revolutions. However in this work, the CoHP simulation was initialised directly from RANS solutions used to verify the geometrical modifications. Using this methodology, convergence was achieved within only 3 impeller revolutions saving up to 140,000 core hours with respect to the initialisation from a flow at rest. This CoHP simulation was then run until convergence and then for 10 rotations for analysis. The CC configuration was initialised from conditions at rest with first a mono-species non-reactive flow to converge the aerodynamics and design point at reduced cost. Once the solution is converged after approximately 20 ms, the gas air (represented by a single species in AVBP) is transformed into a mixture of N2, O2 and the species: CO, CO2 and H2O, which are set to zero. Then fuel is injected in a gaseous form inside the vaporiser for about 5 ms until a recirculation zone of mixed fuel and air is generated in the combustion chamber. The flow is then ignited by adding an energy deposition that mimics a spark. To finish, the simulation is converged after a transient period of about 25 ms with a flame properly positioned in the flame-tube. Data is then acquired for 50 additional milliseconds for flow analysis which corresponds to about 5 convective flow-through times which is enough to converge root-mean-square (RMS) values.
Generation of the integrated domain and associated mesh
The static sub-domain for FULLEST is composed of the OGVs, the bypass duct, the radial and axial diffusers as well as the combustion chamber as illustrated in Figure 1e. Furthermore, it is geometrically divided in aft and forward disconnected regions by the impeller sub-domain. The mesh and initial solution of the fan sub-domain, the forward region of the static sub-domain (from fan outlet to compressor inlet) and the impeller sub-domain can be easily constructed by azimuthal repetition of sectoral meshes using the in-house package for manipulating unstructured computational grids HIP (Müller, 1999). The tool HIP is able to merge all replicated surfaces creating a single mesh and associated solution file for all 360° sub-domains. In fact, only the mesh for the fan sub-domain from FAN + OGV is conserved intact. The sectoral meshes for the OGVs and bypass duct regions are first regenerated with the same refinement parameters as FAN + OGV, taking into account the right geometry connecting to the impeller. For the impeller sub-domain, a new sectoral mesh is created with new refinement parameters. Then, the mesh for the fan sub-domain and the one regenerated for the OGVs and bypass duct region can be repeated 13 times and rotated while the impeller can be duplicated 10 times.
A particular challenge arises for the aft region of the static sub-domain, i.e. the diffusers and the combustion chamber because they differ in their azimuthal periodicities. For this specific static component junction, if the sectoral meshes were to be repeated azimuthally, a non-conformal interface (not supported by AVBP) would appear between the axial diffuser and the combustion chamber regions. Several solutions were considered to overcome this problem. The generation of a fully 360 degrees refined mesh including the diffusers and the combustion chamber was discarded due to memory limitations to generate such a heavy mesh on our visualisation machine with 64 GB of RAM. The addition of another AVBP instance for the combustion chamber was also tested on a sectoral configuration but it led to an increase in computational cost of over 20% due to the additional instance and its new interfaces. Ultimately, the solution retained for this work was to generate a 360 degrees coarse mesh that was then refined following a given metric using the library MMG (Dapogny et al., 2014; Daviller et al., 2017). To refine and adapt the mesh, a metric is constructed using the meshes from the stand-alone sectoral simulations as the target mesh (Figure 3a), and using the 360 degrees coarse mesh as input (Figure 3b). The metric is then applied to the local edge size of the cells and it is computed by dividing the cell-averaged edge size of the coarse mesh by the target edge size of the sectoral simulation at each node of the coarse mesh. The edge size value of the target mesh is interpolated on the coarse mesh in order to be able to perform this operation. The mesh adaptation was performed only on the aft region of the considered sub-domain (static sub-domain of CoHP + CC) and due to other technical limitations (currently, MMG is only capable of handling 32-bit integers limiting the size of the domain it can handle), the sub-domain was further divided in 8 zones as depicted in Figure 3b by the red boundaries. Each zone is therefore adapted independently and then merged together with HIP. In order to do so and avoid non-matching interfaces, the boundaries of each zone are generated to the target sizes of the initial coarse mesh and are not modified during the adaptation process. Finally, the full static sub-domain for FULLEST is obtained by adding together both aft and forward regions. A view of the resulting mesh for the combustion chamber is illustrated in Figure 3c. Although cumbersome, this procedure was the only way to generate this extreme mesh.
Setup of the initial solution for the integrated domain
As mentioned above, the initial solution file for the forward region of the engine (including the impeller) was generated by an azimuthal duplication of the last instantaneous converged results from the corresponding stand-alone simulations. Prior to this duplication, the number of species is again transformed following the same procedure as the one used in the stand-alone CC, i.e. change from the mono-species air to the mixture of species used to model combustion and then interpolated in the intermediate sectoral meshes mentioned above for the fan, OGVs and impeller. This is also performed in the axial and radial diffusers. The solution for the aft region (diffusers and combustion chamber) is then obtained in a similar manner as Pérez Arroyo et al. (2020) by performing two partial piecewise linear gradient-based interpolations. First, the CC solution is azimuthally repeated and partially interpolated into the 360 degrees refined CoHP + CC mesh. Then, in the second step, the azimuthally repeated solution from the diffusers is partially interpolated onto the CoHP + CC mesh, where the previously interpolated solution is also read and overwritten in the axial diffuser as well as part of the contouring casing.
Efficient mesh partitioning for the integrated domain
Finally, the mesh and associated solution need to be partitioned in order to launch the simulation in parallel. This was performed for FULLEST utilizing the hierarchical domain decomposition and load balancing tool TREEPART (Mohanamuraly and Staffelbach, 2020). Indeed, FULLEST is out of scope of standard domain decomposition techniques due to the large number of elements and the large number of cores used in the simulations. Traditional domain decomposition libraries such as Parmetis (Karypis and Kumar, 1998) or Pt-Scotch (Chevalier and Pellegrini, 2008), often fail with core counts over 4,000 and with meshes over 700 M elements in the author's experience. This is due to the important memory requirements and global communications used in these libraries. TREEPART was built to account for the local computing machine topology at the hardware level and minimise global communications. In fact it uses one-side MPI 3 communications for all exchanges and only relies on Parmetis for low level graph decompositions. TREEPART can be used at runtime within the code or off-line to generate a parallel mapping file called el2part (each element of the mesh is mapped to a given number of partitions) than can be read by AVBP to perform the simulation reducing initialisation times and ensuring reproducibility. An illustration of the final partitioning is shown in Figure 4 (left).
Figure 4.
Three-dimensional illustrations of FULLEST. (left) Illustration of the partitioning over 8,820 cores for the static domain (in blue colours), 2,880 cores for the compressor instance (in green colours) and 2,688 cores for the fan instance (in yellow colours). (right) Instantanous contours of FULLEST depicting Mach number in the forward region, density gradients in the compressor, pressure fluctuations in the contouring casing and temperature in the combustion chamber.

From sectoral and stand-alone to 360 degrees and integrated simulations
The simulation is initialised on the CoHP + CC domain for 6 impeller revolutions in order to ensure that the flow is correctly established between the compressor stage and the combustion chamber at a reduced cost. After this time, the remaining forward section of the engine is added (FULLEST case) and the simulation is run for 26 additional impeller revolutions to eliminate the transient related to the integration from the whole domain and acquire data for analysis. The complexity of this simulation is demonstrated in Figure 4 (right) with an instantaneous snapshot of the entire domain. Figure 5 illustrates the convergence of integral values at 4 axial locations in the domain (see Figure 1e): at the outlet of the secondary flow, at the inlet of the compressor, at the exit of the axial diffuser and at the exit of the combustion chamber. Results are normalised with the zero-dimensional values at those sections. These are averaged quantities in time (steady values) and space (e.g. over an axial plane at the inlet of the machine). These values are used to define the main characteristics of the engine in a design process. The outlet of the secondary flow (Figure 5a) features a transient in mass-flow rate
Figure 5.
Convergence plots of normalised integral values for (solid black) m ˙ , (dash-dotted red) T t and (dashed blue) P t at four different cross-sectional positions noted in yellow in Figure 1e. Values are normalised by the ones from the thermodynamic cycle. (a) Secondary flow outlet. (b) Impeller inlet. (c) Axial diffuser trailing edge. (d) Combustion chamber exit.
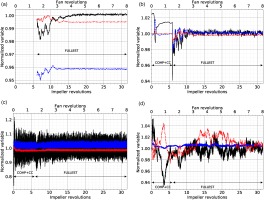
Table 2 shows the comparison against the design operating point for both stand-alone and integrated simulations computed over the last 10 impeller revolutions at different positions of the engine for
Table 2.
Relative errors of zero-dimensional values for mass-flow, total temperature and pressure between the simulations and the designed operating conditions.
During the initialisation, the flow does not only experience the transient developed from adding other components but also an azimuthal decorrelation. This occurs because the initial solution has been azimuthally repeated from the sectoral simulations. This decorrelation is illustrated in Figure 6 using temporal signals extracted from nodes at similar axial locations as the ones used for Figure 5. The decorrelation is calculated by computing the evolution of the Pearson correlation coefficient,
Figure 6.
Azimuthal decorrelation plots of local signals for (black) u x , (red) T and (blue) P at different positions noted in red in Figure 1e. Solid lines represent the decorrelation with the adjacent azimuthal sector whereas dashed lines illustrate the decorrelation with the opposite azimuthal sector. (a) Secondary flow outlet. (b) Impeller inlet. (c) Exit of the axial diffuser. (d) Combustion chamber exit.
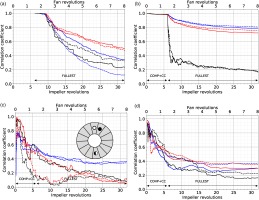
where n goes from 1 to the total number of iterations N computed in the simulation. The signal
Upstream propagating shock-wave from the compressor
The flow topology generated at the inlet of the impeller is presented since it has an impact on the flow around the fan and OGVs. At take-off conditions, the compressor operates in transonic conditions in the rotating frame of reference of the impeller and a shock-wave is formed at the leading edge of the impeller which propagates upstream towards the fan. The shock is generated due to the high impeller rotational speed needed to attain the designed pressure ratio at take-off (Ferri, 1964). The flow field is therefore dominated by a strong shock as depicted in Figure 7 using an instantaneous field at 70% of the normalised hub-to-shroud distance (denoted hereafter
Figure 7.
Illustration of the upstream propagating shock at 70% h / H generated at the leading-edge of the impeller. Black iso-line refers to the sonic line in the relative frame of reference.
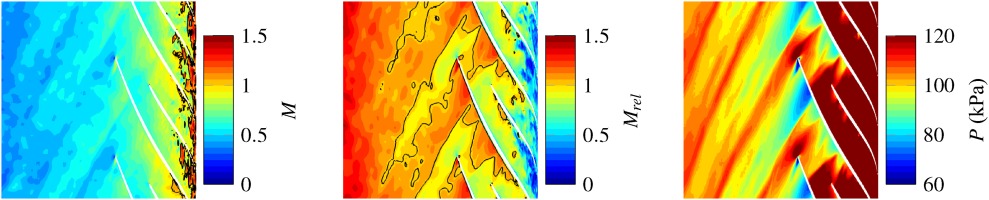
Since the shock is anchored at the leading edge of the impeller, it rotates with it. This discontinuity is seen as a propagation in the absolute frame. Disturbances that propagate at subsonic conditions are known to decay exponentially with distance, however, because shock wave evolution is principally an inviscid phenomenon as demonstrated by Prasad (2003), it decays as the inverse of the axial distance from the leading edge (Morfey and Fisher, 1970; Hawkings, 1971). Indeed, far from the rotor and for high pressure jump ratios noted
where
Figure 8.
Normalised pressure jump Π at different values of h / H : (yellow) 10%, (green) 30%, (cyan) 50%, (violet) 70%, (red) 90%. (solid) FULLEST, (dashed) FAN + OGV. (∙ ) analytical expression (Equation 2).
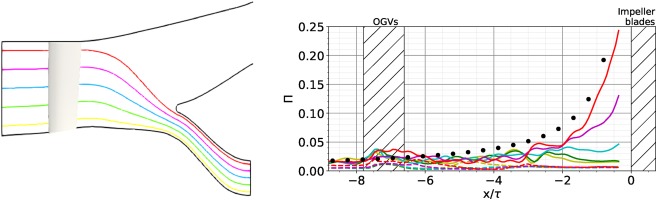
Conclusions
The integrated reactive large-eddy simulation with over 2,100 million cells of a 360 azimuthal degrees gas-turbine including the fan, radial compressor and annular chamber is presented as a means to investigate three main topics: first, the feasibility in terms of cost and methodology of such massive simulations; second, generate a three-dimensional data-base composed of the stand-alone components and the integrated simulation; and third, analyse the effects of the integration of several components thanks to one single simulation.
The configuration of study DGEN-380 is not CFD-friendly in terms of periodicity between components, i.e. the greatest common divisor between blades, vanes and the sectors of the combustion chamber is 1. Indeed, industrial turbomachinery uses coprime integers for the blade numbers to avoid resonance phenomena and to control the acoustic modes propagated in ducts (Tyler and Sofrin, 1962). In order to reduce the complexity of the problem, the engine has been split in three components: fan and OGVs; centrifugal compressor, including radial and axial diffusers; and combustion chamber. These components have been adapted to a CFD-friendly geometry independently resulting in three different periodicities (1 per component). The methodology introduced by Pérez Arroyo et al. (2020) is then extended to a 360 degrees domain and multiple components of the engine. The CFD-friendly stand-alone components are simulated independently and converged at a relative low cost on periodic domains and then interpolated onto the mesh of the 360 degrees integrated domain which conserves the azimuthal periodicity of each component. Without the prior adaptation of each component to CFD-friendly domains, this methodology could not be applied and the integrated simulation would be initialised from scratch since the solution for each component would not be available. Besides, it enables a fair investigation of the impact of such an integration since they now have the same periodicity for each component. In this work, this procedure saves about 8 million core hours with respect to an initialisation from scratch and in addition generates a data-base of stand-alone component predictions.
Without considering the optimisations for parallel computing and the ability of the code to perform such simulations, the main challenge to overcome has been the generation of the 2,100 million cells mesh for FULLEST. This mesh has been generated in several steps to surpass present memory and software limitations encountered in our work. The generation of the mesh for some of the sub-domains such as the fan, the OGVs and the impeller takes advantage of the initial periodic mesh which is simply repeated azimuthally using the in-house package for manipulating unstructured computational grids HIP (Müller, 1999). This fast mesh generation process is not possible for the forward region of the domain since the diffusers and the combustion chamber do not share the azimuthal periodicity. Instead, the mesh is generated through a complex method of adaptation of a 360 degrees coarse mesh into a refined mesh using the MMG library. Additional tools or extended capabilities in existing mesh generators should continue to be developed to simplify this process since this kind of complex simulations (with different periodicities and components) will be performed regularly in the near future.
The 360 degrees simulation is initialised from the (interpolated) azimuthally repeated sectoral instantaneous solutions of each component and thus at the start, it is identical for each azimuthal sector. This has been analysed by computing the evolution of the correlation between temporal signals at different azimuthal positions. It can be concluded that the flow decorrelates at different rates depending of the location of study. Where the perturbations are smaller like the outlet of the secondary flow, the decorrelation has not yet converged but it is achieved within several impeller revolutions at locations downstream of the compressor. This needs to be considered for example if acoustic measurements are performed and the plane at the exit of the secondary flow is used as source to propagate to the far-field or when azimuthal modes are investigated throughout the machine. In addition, the interpolation performed on some sub-domains generates a transient of mass-flow but it is recovered within several fan revolutions, which is faster than the time the flow needs to decorrelate. Both stand-alone and integrated simulations are able to predict physical results and they correctly achieve the expected thermodynamic cycle of the engine with an overall error below 1%. The impact of the integration on the zero-dimensional values is minimal and only of relevance at the exit of the compressor and inlet of the combustion chamber due to the different boundary conditions. Nonetheless, the integrated simulation FULLEST recovers values of total pressure and temperature in agreement with the exit of CoHP and the inlet of CC, respectively.
Finally, it is concluded that the integration of several components of an engine with LES is challenging but yet feasible. The authors acknowledge that the cost for such 360 degrees LES is still high and possibly limited to big corporations or would require special access to supercomputing resources. This work is a first step towards the LES of a full digital twin of the engine where the turbine stages and the exhaust jet are also considered.
Nomenclature
Symbols
Specific heat ratio (−)
Normalised hub-to-shroud distance (−)
Mass-flow (kg/s)
Mach number (−)
Axial Mach number (−)
Relative Mach number (−)
Static pressure (Pa)
Total pressure (Pa)
Normalised pressure jump across the shock (−)
Pitch between blades (m)
Static temperature (T)
Total temperature [K]
Axial velocity (m/s)
Dimensionless wall-coordinate (−)
Acronyms
CFD
Computational Fluid Dynamics
CWIPI
Coupling With Interpolation Parallel Interface
FULLEST
First fUlL engine computation with Large Eddy SimulaTion
LES
Large-Eddy Simulation
OGV
Outlet-guide vane
PSD
Power Spectral Density
RANS
Reynolds-Averaged Navier-Stokes
RMS
Root-mean-square
SPMD
Single Program - Multiple Data
URANS
Unsteady-RANS